Kooperation für nachhaltige Mobilität
Es wird elektrisch auf den Straßen der Welt. Autobauer und Zulieferer sind längst auf diesen Zug aufgesprungen. Doch der Engineering-Partner IAV will diesem Trend nicht einfach nur folgen, sondern den Wandel aktiv mitgestalten. Deshalb entwickelte das Unternehmen aus Berlin einen eigenen vollelektrischen Antriebsstrang – mit Wieland als Partner.
Ein leistungsfähiger Kompetenzträger, der skalierbar und serientauglich ist - das war das Ziel, das sich IAV gesteckt hatte. Für die Entwicklung des Elektromotors im Antriebsstrang arbeitete das Unternehmen zunächst mit lokalen Fertigern zusammen. Schnell wurde jedoch klar, dass gängige Fertigungsmethoden des Kurzschlusskäfigs in der Asynchronmaschine mit Kupferläufer strukturelle Probleme mit sich brachten. „Weder Gießen noch Löten des Rotors im Käfig bringen die gewünschten Ergebnisse. Wir haben dann mit Wieland gesprochen, wie man den Prototyp umarbeiten kann, so dass er mit den Wieland-Werkzeugen lasergeschweißt werden kann“, erzählt Jens Liebold, Fachreferent für Elektromechanische Antriebssysteme bei IAV.
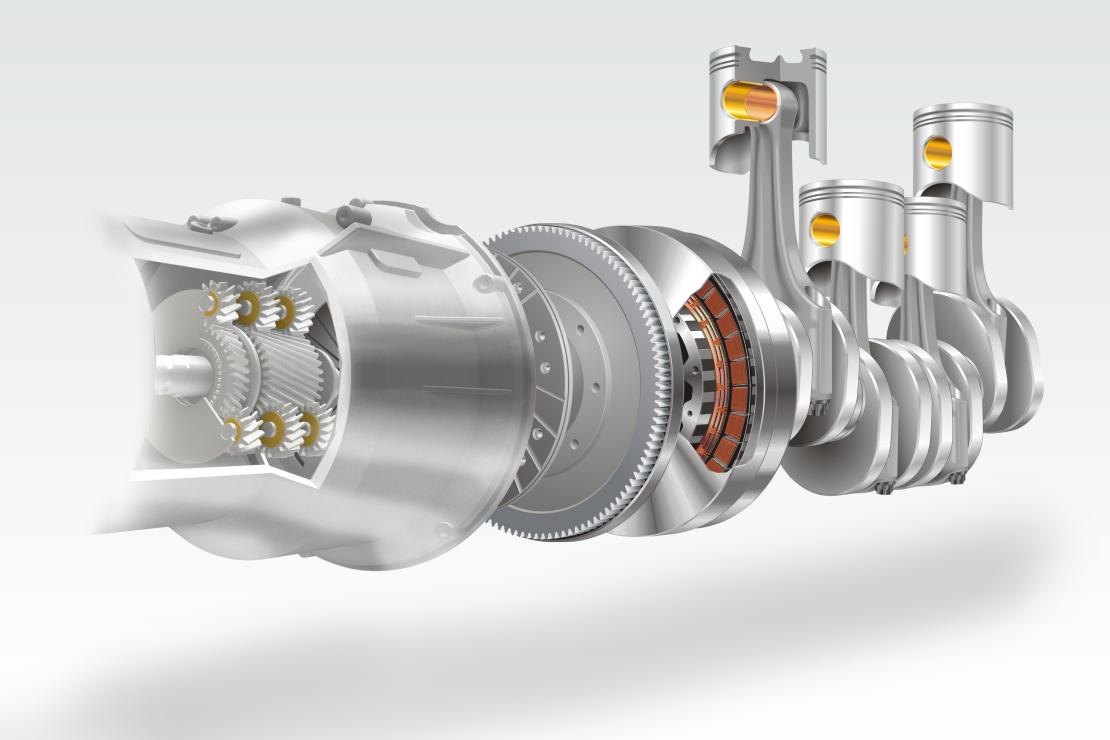
Querschnittsbild der E-Maschine
Neben den Fertigungsmöglichkeiten war die Kupferwerkstoffexpertise von Wieland für die Wahl ausschlaggebend. „Die grundsätzliche Idee war, den Teil des Rotors, der für die Drehmomentbildung zuständig ist, aus Kupfer zu fertigen, weil Kupfer im Gegensatz zum üblicherweise eingesetzten Aluminium ein besserer elektrischer Leiter ist“, erklärt Liebold.
Ein patentiertes Design bringt Leistung
Wieland nahm sich der Herausforderung gerne an. Schon früh hatte das Unternehmen den Trend der Elektromobilität erkannt und konnte über Jahre Erfahrungen in dem Bereich sammeln. „Wir haben für IAV ein komplett neues Rotor-Design entwickelt“, erklärt Michael Wolf, Team Leader Business Development eMobility bei Wieland. Das patentierte Design erlaubt im Vergleich zu herkömmlichen Rotoren zudem deutlich höhere Drehzahlen, was den gesamten Antriebsstrang leistungsfähiger macht. Auch in der Herstellung hat der Wieland-Rotor deutliche Vorteile. Einzelteile wie Rotorstäbe und Endringe lassen sich einfach, schnell und vergleichsweise kostengünstig in großer Stückzahl herstellen. Durch das Laserschweißen kann schneller produziert werden, denn das Material wird nur lokal hoch erhitzt, folglich gibt es kürzere Kühlungszeiten und folgende Prozessschritte können schneller erfolgen. Außerdem ist der Aufbau so flexibel, dass er leicht skalierbar ist. Für Anwendungen im Hochleistungsbereich können unterschiedliche Material-Kombinationen im Endring zum Einsatz kommen.
Von individuellen Systemkomponenten für Elektromotoren, über Kontaktträger in permanentmagnetischen Synchronmotoren und gefertigten Kupferrotoren in Asynchronmaschinen, bis zu Spezial-Bimetallen, insbesondere für elektrifizierte und hybride Automobil-Antriebsstränge — Wieland entwickelt Komponenten für alternative Antriebstechnologien und begleitet die Branche mit einem hohen Maß an Kompetenz von der Entwicklung bis zur Großserienfertigung.
Mehr über Komponenten für die E-Mobilität
Partnerschaft mit Zukunft
Seit diesem ersten gemeinsamen Projekt arbeiten Wieland und IAV regelmäßig zusammen. „Wir tauschen uns über den Stand der Technik aus und besprechen neue Kooperationen auf Forschungsseite. Und wir überlegen, welche Fertigungstechnik von Wieland uns helfen kann, unsere Elektromotoren noch besser zu machen“, sagt Liebold. Die Zusammenarbeit bei der modularen elektrischen Antriebseinheit hat sich jedenfalls ausgezahlt. Mit Hilfe von Wieland gelang es IAV, für ihre Kunden eine Asynchronmaschine mit integriertem Differential zu entwickeln, die effizienter und höher performant ist, als sie es mit herkömmlichen Rotor-Technologien wäre. Die Lösung ist zudem bei einer größeren Serie mit hohen Stückzahlen äußerst wirtschaftlich.
Auf einen Blick
- Der Engineering-Partner IAV brauchte für die Entwicklung eines elektrischen Antriebsstrang eine neue Lösung für einen Kupferrotor.
- Wieland entwickelte ein leistungsfähiges, patentiertes Rotor-Design, das skalierbar und äußerst wirtschaftlich in der Produktion ist.
- IAV kann seinen Kunden eine effiziente und flexible Lösung anbieten.