Data sheet
Wieland GEWA-D Finned Tubes
Medium high finned tubes for compact coiled and bent heat exchangers
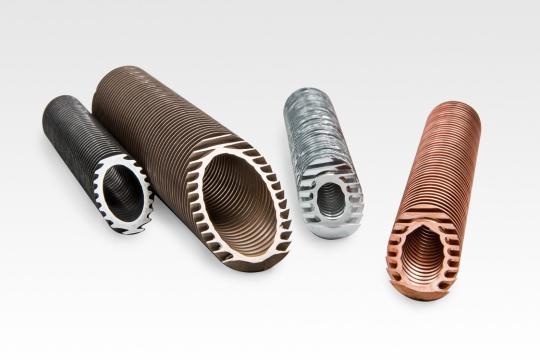
Wieland GEWA-D tubes are medium high finned tubes in copper and copper alloys as well as aluminum, carbon or stainless steel. Finned tubes of this series resist very high mechanical and thermal stress.
For improved heat transfer the inner surface of GEWA-DW tubes have an additional structure. This also favors very small bending radii and coil diameters.
Tube number | Alloy* | Tube type** | Outside diameter [mm] | Fin height [mm] | Inside diameter [mm] | Outside diameter plain end [mm] | Outside surface area [m2/m] | Approx. weight [kg/m] |
D-1135.12100-00 | K21 | D | DW | 19.00 | 3.50 | 10.00 | 15.00 | 0.18 | 0.62 |
D-1135.14100-00 | K21 | D | DW | 21.00 | 3.50 | 12.00 | 18.00 | 0.20 | 0.72 |
D-1135.18100-00 | K21 | D | DW | 25.50 | 3.50 | 16.50 | 22.00 | 0.26 | 0.94 |
D-1145.18100-00 | K21 | D | 27.50 | 4.50 | 16.50 | 22.00 | 0.33 | 1.04 |
DW-1132.12085-16 | K21 | DW | 19.00 | 3.20 | 10.90 | 15.88 | 0.16 | 0.61 |
DW-1135.18080-16 | K21 | DW | 25.50 | 3.50 | 16.90 | 22.00 | 0.26 | 0.81 |
DW-1133.12079-16 | L10 | DW | 19.05 | 3.30 | 10.87 | 15.88 | 0.17 | 0.57 |
DW-1133.25125-16 | L10 | DW | 31.75 | 3.37 | 22.51 | 28.58 | 0.33 | 1.40 |
D-1135.14175-00 | A22 | D | 21.00 | 3.50 | 10.50 | 16.10 | 0.20 | 0.29 |
DW-1145.11122-16 | A22 | DW | 20.00 | 4.50 | 8.56 | 14.80 | 0.22 | 0.23 |
D-1145.18080-00 | O60 | D | 27.00 | 4.50 | 16.40 | 21.30 | 0.32 | 0.90 |
Fin pitch 11 fins/inch
* K = copper | L = copper-nickel | A = aluminum | O = carbon steel | P = stainless steel
** D = medium high finned + inside undulation | DW = medium high finned + internal structure
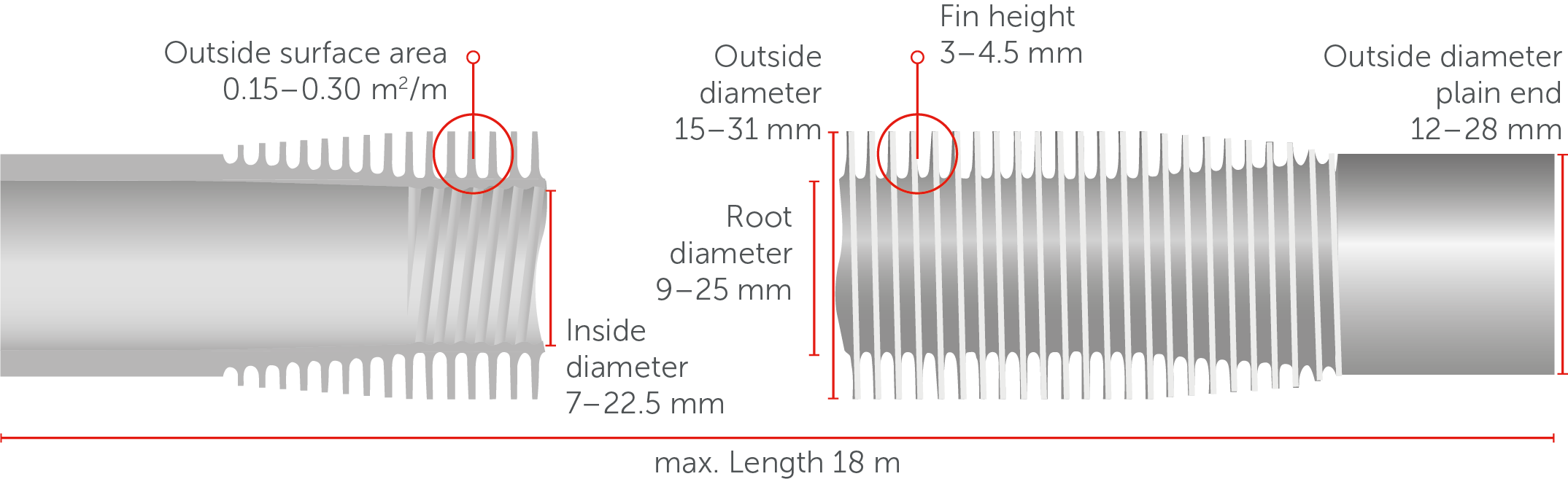
Tube number code system (example D-1135.14100-00)
D- | 11 | 35. | 14 | 100 | -00 |
Tube type | Fins/inch | Fin height [1/10 mm] | Core-tube diameter [mm] | Wall thickness [1/100 mm] | Inner structure
|
Length [mm] | Length tolerances |
< 2,000 | + 2 mm |
2,000 - 8,000 | + 1 ‰ (max 5 mm) |
> 8,000 | + 0.7 ‰ |
Advantages
- optimized inner to outer surface ratio
- availability of different inner structures for optimum operating conditions
- compact designs through high specific heat capacity
- enhanced performance through inner structures
Applications
- heating industry (hot water tanks)
- air conditioning and refrigeration (refrigerant condensers and evaporators)
- mechanical engineering (oil coolers, gas coolers)
- process engineering
Operating range
- high-pressure applications up to 134 bar possible (e.g. R744)
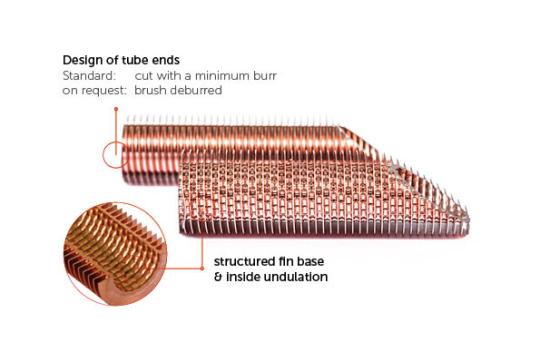
Production and processing
The fins are obtained by roll forming the outer surface of a plain tube. This process results in an increase in strength of the finned sections. Plain ends remain soft and have a smaller diameter than fined sections. Soft annealing of the tubes is necessary if they must be suitable for coiling or bending to heat exchangers.
Wieland Materials | EN-Symbol | Material No. | UNS-No. |
A22 | AW-AlMgSi | EN AW 6060 | - |
K21 | Cu-DHP | CW024A | C12200 |
L10 | CuNi10Fe1Mn | CW352H | C70600 |
O60 | P195GH | 1.0348 | - |
P05 | - | 1.4510 | S43035 |
The primary material complies with the requirements of DIN EN 12451, AD-2000 Merkblatt W6/2 and on request with ASTM B111 or ASTM B75. For aluminum, carbon or stainless steel individually standards agreed with the customer can be applied.
GEWA-D finned tubes are manufactured acc. to Wieland standard R-2200 and DIN EN 12451. On request, a production acc. to VdTÜV 420/2 (harmonized with the European Pressure Equipment Directive PED 2014/68/EU) or ASME SB 359/ASTM B359 is possible.
Quality Assurance
To ensure consistent product quality, Wieland-Werke AG has a sophisticated quality control system according to DIN EN ISO
9001:2015 which has been verified and certified by an independent certification company. Our test laboratories in the Central Laboratory and Development Services have been accredited to DIN EN ISO/IEC 17025:2018 and DIN EN ISO 9001 as test and certification laboratories.
Technical Service
Our Technical Marketing experts are available at any time as contact partners to work together with your experts from the
very early product planning stages in order to obtain optimum results for the manufacturing stage and for your application.
The only way to find the best, most cost-effective solution is by means of comprehensive technical consultation based on
computerised thermal engineering rating.