Strips, sheets and plates made of copper, brass, bronze, nickel silver and aluminium
Your specialist for copper and copper alloys – worldwide
As one of the world's leading suppliers of semi-finished products made of copper and copper alloys as well as other materials such as aluminum, titanium and steel, we support your success with reliable, flexible supply and the best service at consistently high quality. Our products, services and technologies provide sustainable and innovative solutions to today's global challenges such as climate change, digitalization and resource conservation.
Listening closely is key to us so we can offer you exactly what you need. Together, we develop solutions for automotive, aerospace, electronics, refrigeration, air conditioning, and many other industries. We use high-performance copper materials to drive your success in future-oriented fields such as electromobility, connectivity, and urbanization. We take you from the idea phase to production readiness – and beyond. High technical competence, customer-oriented thinking, and sustainability determine our actions and have been the basis of our success since 1820.
Global proximity you can count on
With more than 80 locations worldwide, we are always close to you. A strong network of production sites, service and trading companies is there for you with our broad product, technology, and service portfolio in the major European, U.S. and Asian markets:
- reliable supply in your proximity
- excellent service
- consistently high quality
About us – Wieland Group
employees*
locations
€ million operating EBITDA
€ million turnover
€ million investments
* Average number of employees of the Wieland Group in the 2023/24 fiscal year, including 50% of the employees of Schwermetall Halbzeugwerk GmbH & Co. KG
[Fiscal Year 23/24 figures
of the Wieland Group]
Upcoming Events
06.07.2025
WE WANT YOU
Neu-Ulm, Germany
09.07.2025
- 11.07.2025
FAMETA
Stuttgart, Germany
15.07.2025
- 16.07.2025
The Battery Show Asia
Hong-Kong, China
Our products
Choose the right product for your application from our wide range. We are happy to advise you.
Our materials
We offer a wide range of materials to suit your needs. We are here to help.
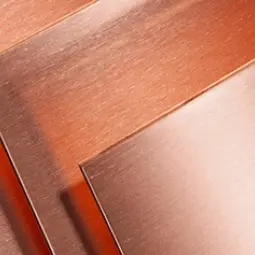

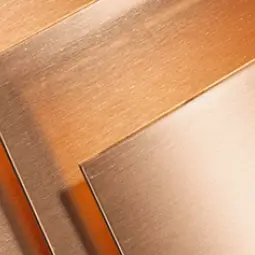
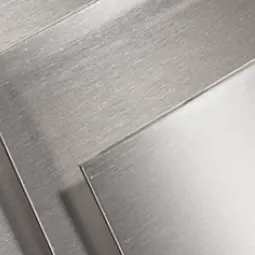
Together for a sustainable future
Sustainability is part of the Wieland Group's core business. Today, we are in the middle of a transformation process that places high demands on us. We are measured not only by our immediate business goals, but also by the expectations of future generations. That is why we have set ourselves ambitious goals in the areas of environmental, social and governance (ESG) in our sustainability strategy.
Career at Wieland
Unleash potential
For over 200 years, we have been shaping the future of copper and copper alloys with 8,800 colleagues at more than 80 locations worldwide. How do you see your future?
Surprise us with your fresh thinking and new ideas, and help us shape the world of tomorrow. At Wieland you will find a wide range of opportunities to unleash your potential - seize your career opportunity now!
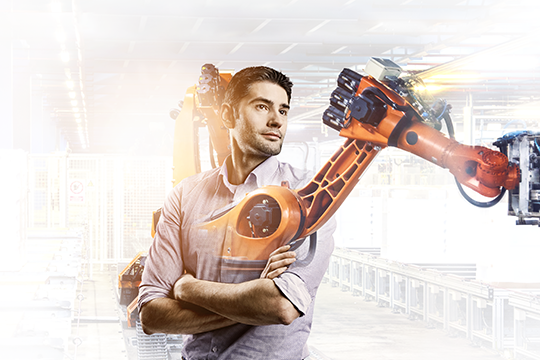

Already know your search term? Then go ahead and use our full text search. You will get a list of all relevant results.