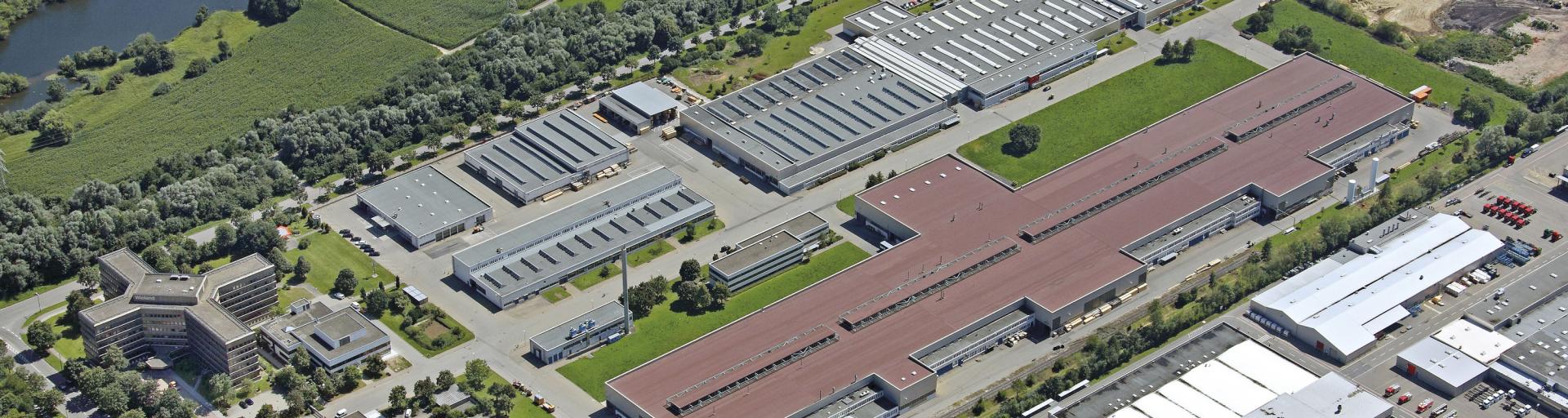
Wieland-Werke AG
Organization
89079 Ulm
Germany (UTC+1)
7:00 am - 5:00 pm
7:00 am - 11:30 am
12:45 pm - 2:30 pm
Facts
employees
covered area m²
over all area m²
Metal Information
Current metal prices
Locations
Global proximity you can count on

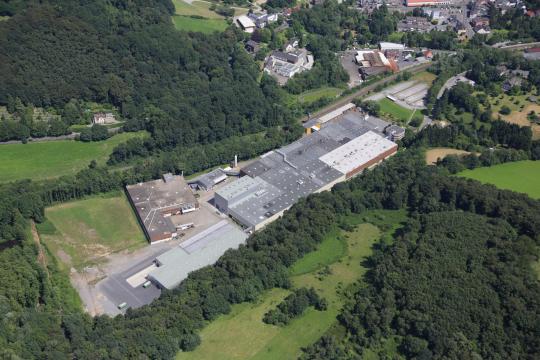
Wieland-Werke AG – Velbert
Wieland-Werke AG
Ziegeleiweg 20
42555
Velbert
Germany
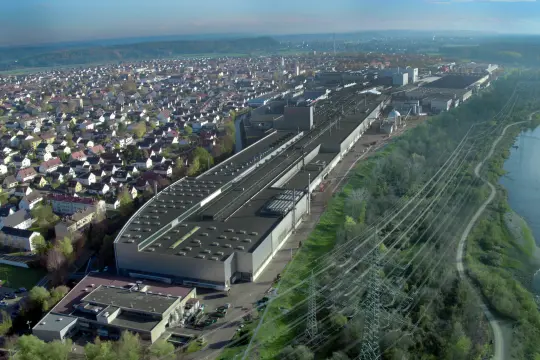
Wieland-Werke AG – Vöhringen
Wieland-Werke AG
Wielandstraße 26
89269
Vöhringen
Germany
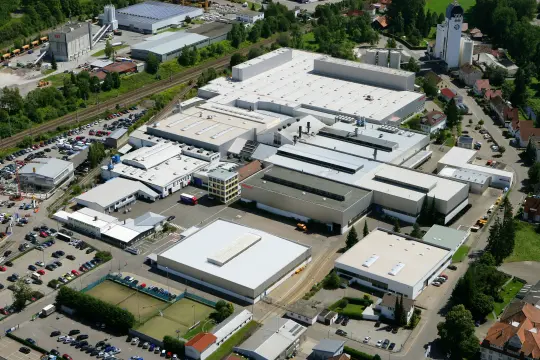
Wieland-Werke AG – Villingen-Schwenningen
Wieland-Werke AG
Lantwattenstraße 11
78050
Villingen-Schwenningen
Germany
Products
Our products at a glance
Product categories
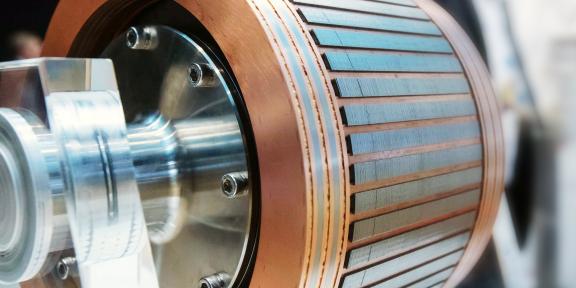
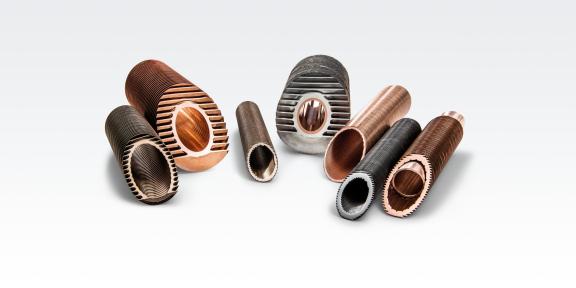
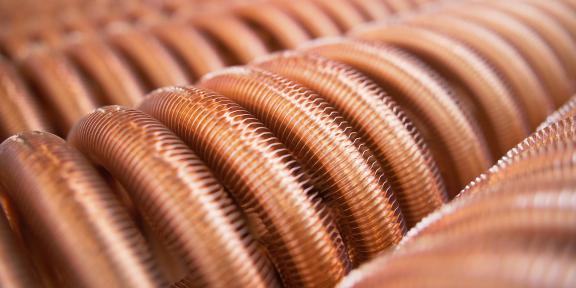
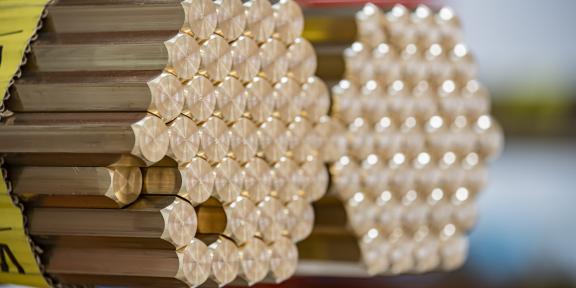
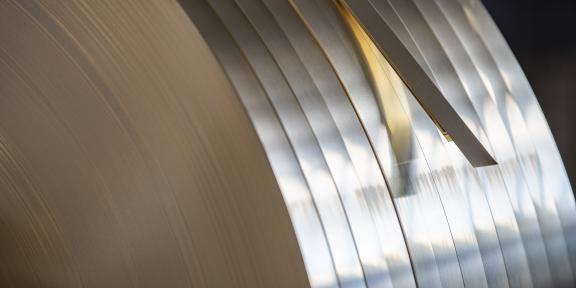
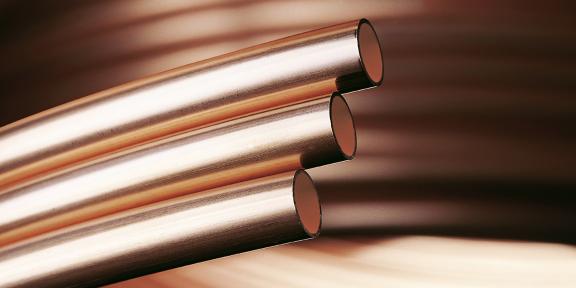
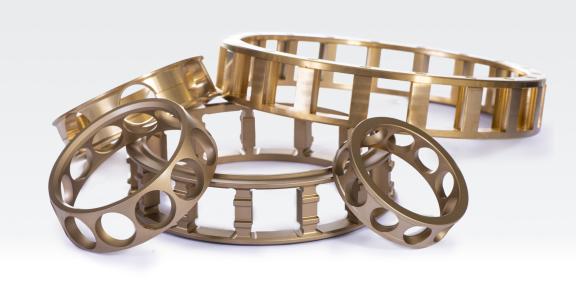

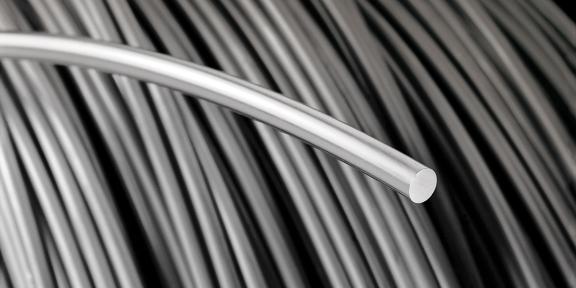
Headline
Back to product overviewRotor Components
Rotors
Overmolded Busbars
Welded Multi-Metal Strips
Shunts
Shunt-based Current Sensors
Enhanced surface tubes
Low-finned tubes
Medium-high finned tubes
High finned tubes
Safety tubes
Coaxial heat exchanger WKE | WKC
Wieland WRK
Wieland safety heat exchanger
Finned tube heat exchanger WRW
Customized heat exchangers
Rods
Sectional rod
Machining
WICONNEC®
ecoline®: Lead-free solutions
Precision continuous casting
Forging Stock
Strip
Hot-dip tin coated strip
Multi-gauge strip
Sheets and Plates
Smooth industrial tubes
Innergrooved industrial tubes
Plumbing tubes
Refrigeration and medical gas tubes
Alloy tubes
Ball Bearings
Roller Bearings
Surfaces and coatings for rolled products
Wire
WITRONIC®
WICONNEC®
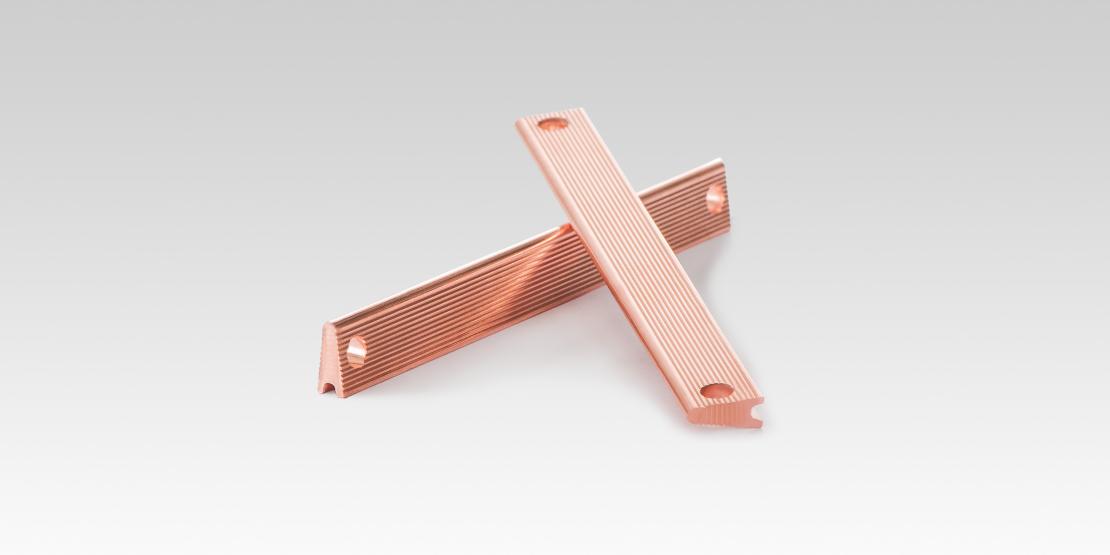
Wieland offers you ready-to-install copper rotor bars of consistently high quality at maximum cost efficiency. This is guaranteed by our fully automated processes across the entire value stream.
In addition, the rotor bars can be manufactured in complex geometries, varying lengths, straight or twisted, and with or without notches. This enables unique rotor designs - from development to series product - from the smallest sample batch to mass production.
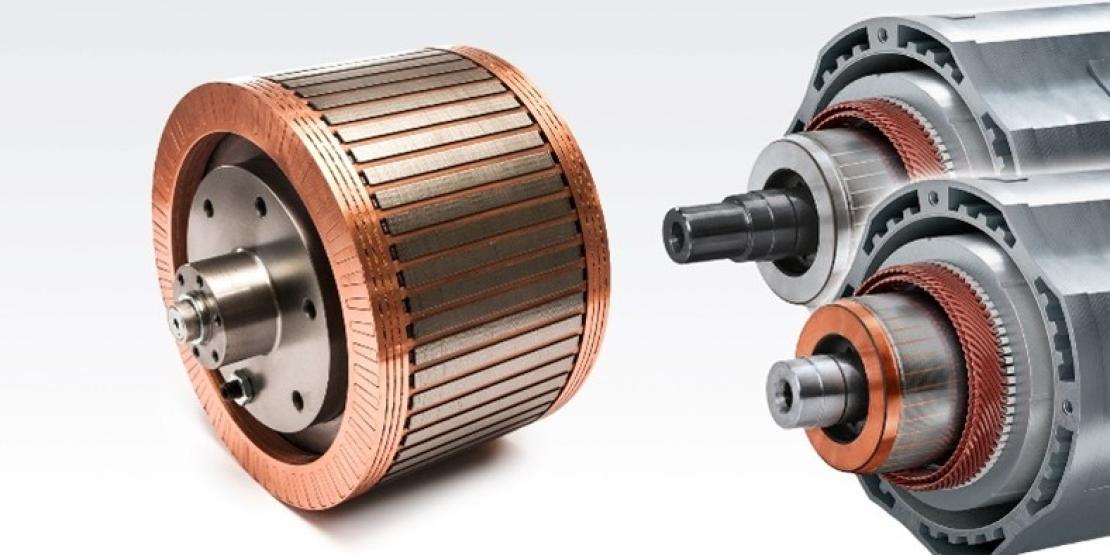
We also offer engineering support during the development of your application-specific design. Furthermore, Wieland offers two different processes to produce rotors to meet your individual requirements. Both processes offer manufacturing with a very high degree of material filling without air inclusions, and we can draw on a wide range of experience from prototypes to series production.
The fabricated Wieland copper rotor is a new and innovative design, which is designed according to your requirements. Due to the disc-shaped design of the short-circuit ring, different materials can be combined individually, and fulfill the requirements for higher power densities and rotation speeds.
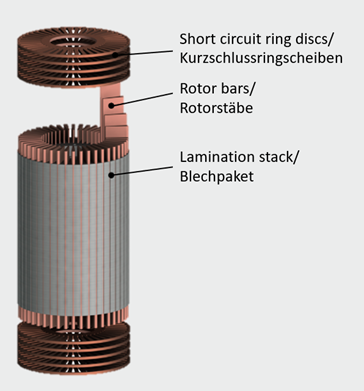
Additionally, the fabricated design has a higher mechanical strength and enables a very scalable, flexible, and economical approach for rotor production.
Overview of possible materials:
(All copper-based materials are produced in-house and are available in various strength levels)
Properties | Wieland K10 | Wieland K14 | Wieland K75 |
Application | Rotor bar | Short circuit ring | Short circuit ring |
Density [g/cm³] | 8,94 | 8,94 | 8,88 |
Electrical Conductivity [MS/m] | ≥58,6 | ≥58 | ≥48 |
Tensile strength Rm [MPa] | 200 – 350 | 220 – ≥360 | 430 – 640 |
Hardness [HV] | 35 – 115 | 45 – ≥110 | 130 – 200 |
Datasheet |
Through our unique and patented Laminar Squeeze Casting technology, Wieland eTraction Systems has succeeded in developing the Zero Porosity Rotor - ZPR®. As shown in the CT scans below, we outperform the industry in both the copper and aluminum rotors.
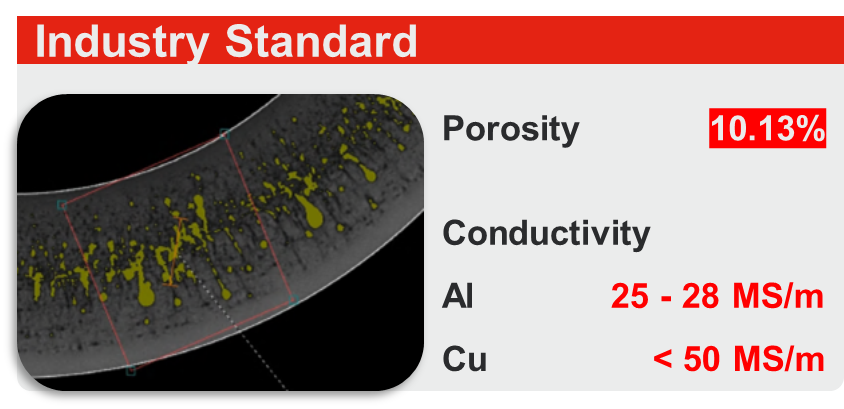
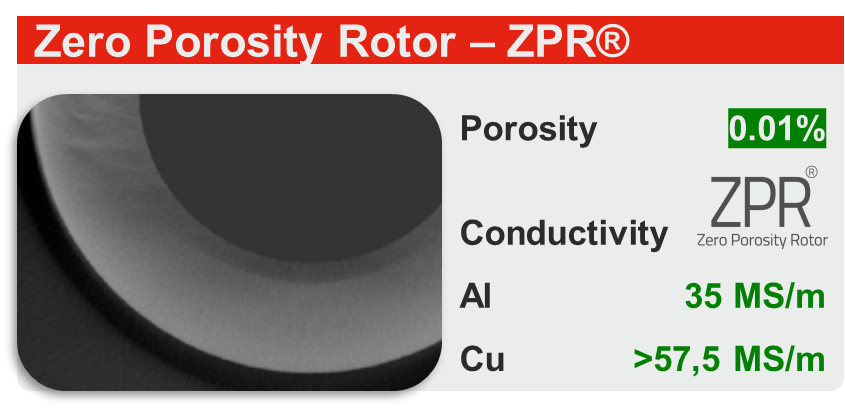
As a result, Wieland eTraction Systems is quality leader within the global rotor manufacturing industry, offering the ZPR® from the smallest sample lot to volume production.
The benefits of a Zero Porosity Rotor - ZPR® are as follows:
- Unique product quality
- Stable process capability
- Significantly higher electrical conductivity
- Higher efficiency of your electric motor
View our brochure to learn more on ZPR
Please enter your contact information. You will be redirected to the download page.
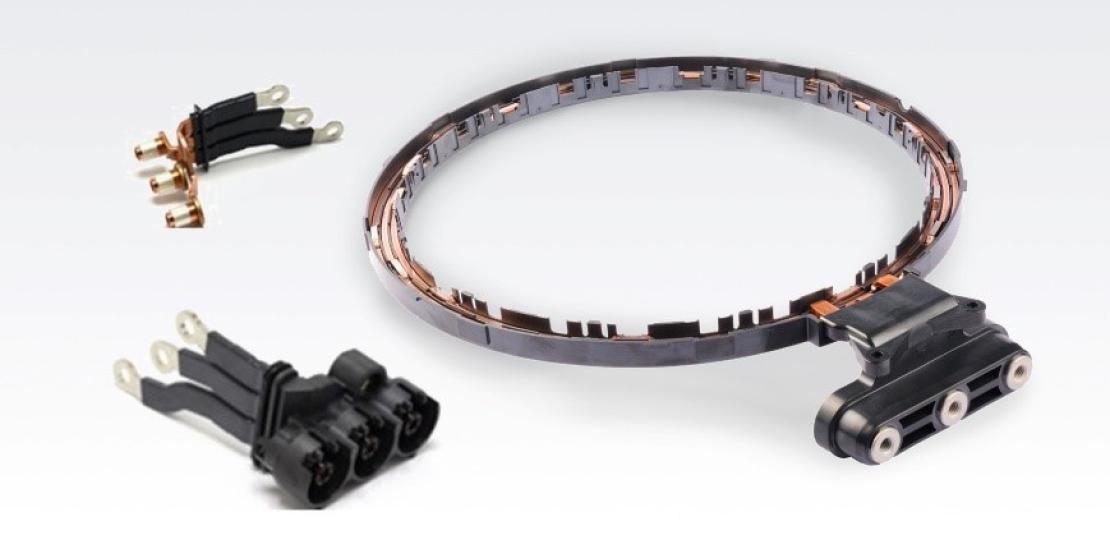
We offer individual solutions and support in development by taking DFM (= Design for Manufacturing) into account and can also offer prototypes from our prototype shop. We are happy to accompany you through all sample phases up to series production.
For contacting in the electric drive train or between the battery and the electric machine, Wieland offers you a wide variety of designs (e.g. fully overmolded; assembled) of ready-to-install connector units and overmolded busbars. The design of these is based on your requirements, which enables contacting in the tightest of spaces.
To evaluate your design and the corresponding requirements, please contact us via the contact address below.
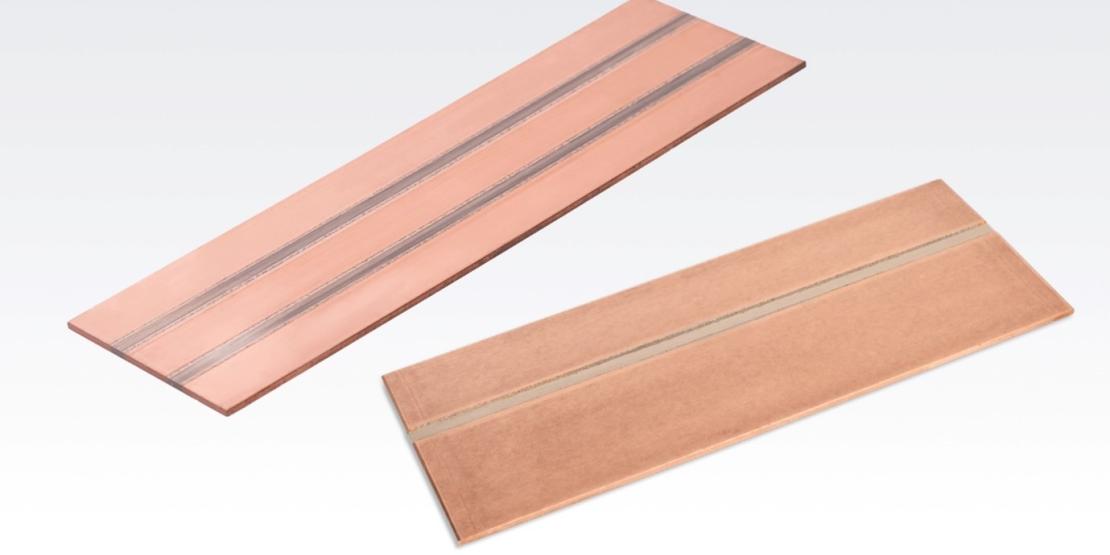
We carry out all process steps in-house, and because of this we can find the best alloy combination for your application. Our offerings don’t end at only using our alloys. We also can evaluate using materials and alloys from other manufacturers.
With the use of our specially developed resistance alloys, electron beam welded multi-metal strips are ideal as pre-material for shunts.
For other applications, we also offer electron beam welded multi-metal strips. This allows the specific properties of several different alloys to be combined and almost any combination of materials is conceivable.
Contact us using the contact address below and we will be happy to review your inquiry and get back to you.
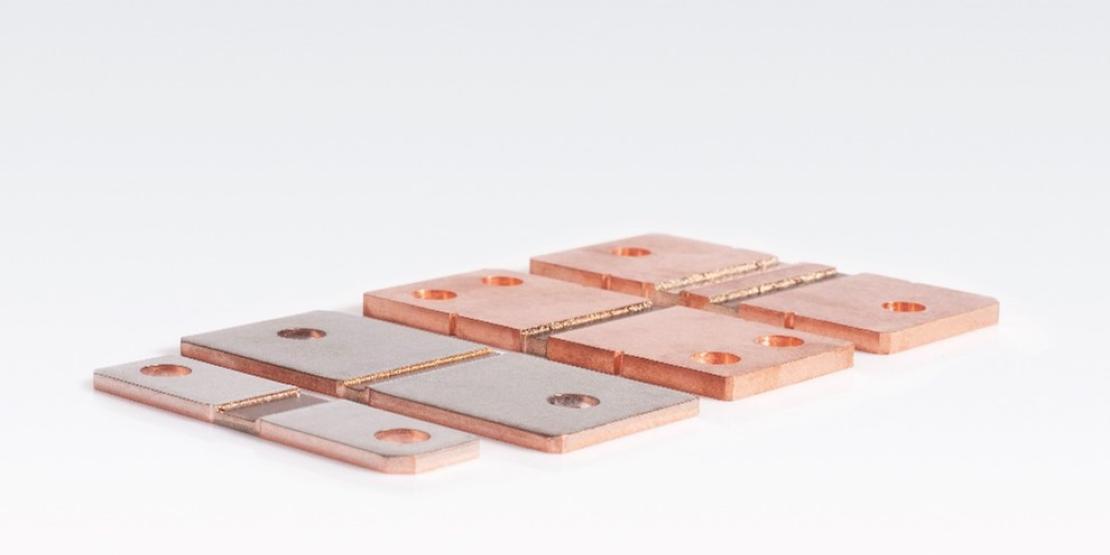
Wieland offers shunts in various standard dimensions as well as customized designs. For this purpose, development, sample, and series production are located in-house.
Our standard shunts are designed according to uniform sizes and resistance values.
Currently, the Wieland portfolio includes the following basic shunts.
Variant | Length [mm] | Width [mm] | Power Rating [W] | Resistance values [µΩ] |
W6918 | 69 | 18 | 36 | 50, 100 |
W8518 | 85 | 18 | 36 | 50, 100 |
W8420 | 84 | 20 | 36 | 50, 100 |
W8436 | 84 | 36 | 50 | 25, 50 |
W8536 | 85 | 36 | 50 | 25, 50 |
View our datasheets to learn more
Please enter your contact information. You will be redirected to the download page.
Wieland also offers customized shunts (e.g. double shunt) designed to your specifications. To evaluate your design and the corresponding requirements, please feel free to contact us via the contact address below.
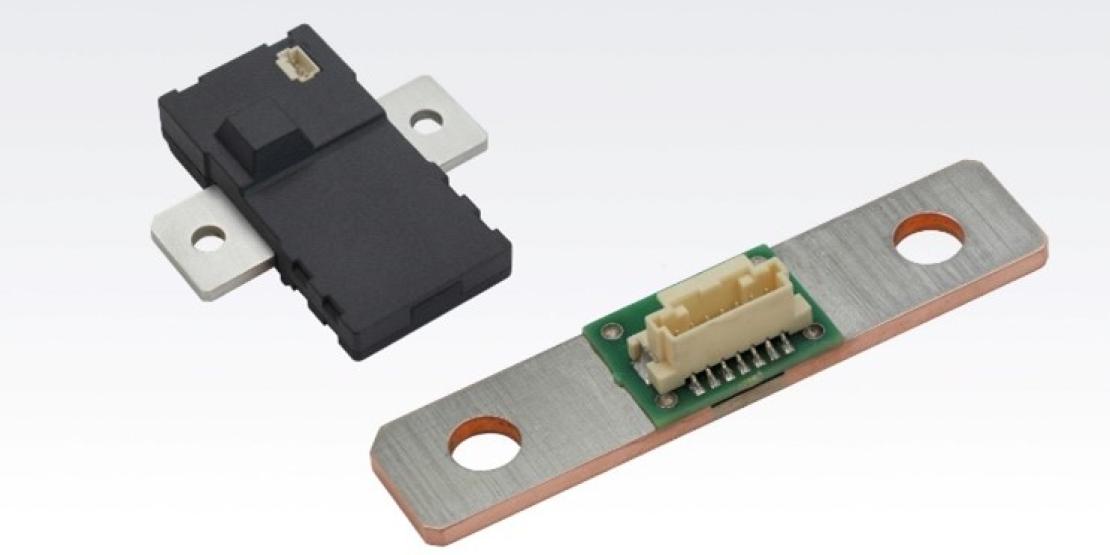
QULECTRA is a joint venture of Wieland-Werke AG based in Ulm and Munich Electrification GmbH based in Munich. The two companies share a multi-year partnership in the provision of battery management systems with shunt-based precision resistors. With QULECTRA, the two companies are taking the next step in the development of best-in-class current sensors that point the way to a sustainable future.
More information about QULECTRA and its products can be conveniently found on the QULECTRA-Website.
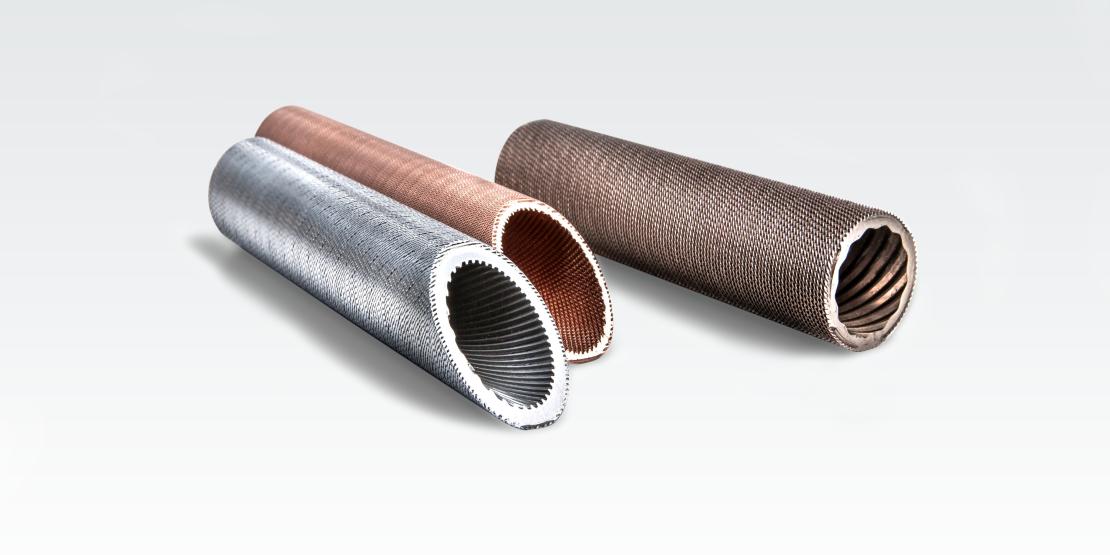
Optimised heat transfer for your shell-and-tube heat exchanger
The enhanced surface tubes made by Wieland Thermal Solutions have been optimized for use as condenser or evaporator tubes in shell-and-tube heat exchangers used in the refrigeration and air-conditioning industry. These can be designed to be much more compact, saving you energy, installation space, and materials.
Your advantages at a glance
- Significantly higher heat transfer coefficients than smooth or low finned tubes
- More compact and lighter heat exchangers
- Significantly reduced filling quantities of e.g. refrigerants
- Highest efficiencies due to smallest temperature differences
- Precise thermal design with ThermalS
Optimized heat transfer for your shell-and-tube heat exchanger
The enhanced surface tubes made by Wieland Thermal Solutions have been optimized for use as condenser or evaporator tubes in shell-and-tube heat exchangers used in the refrigeration and air-conditioning industry. These can be designed to be much more compact, saving you energy, installation space and materials.
Materials
Thanks to their functional surface enhancements, the outsides of the GEWA-C and Turbo-C tubes offer optimal drainage performance for condensed refrigerants. Coupled with an ideally matched inner tube surface, optimum heat transfer coefficients can be achieved. GEWA and TURBO Condenser Tubes are available with outer and inner surfaces adapted for specific needs of your application.
GEWA
- C5 – For highest performance and efficiency
- C+SL/LW – For weight optimized alternatives as a "drop-in" solution
- CLF – For seawater & applications with increased fouling tendency
- CPL – For applications with high fouling tendency
TURBO
- C – The original condenser tube
- CSL – Efficient and lightweight
- CLF – For low fouling applications
- NCT – For large capacity chillers
- CPT – High efficiency in ferrous alloys
The functional enhancements of the outer surfaces of the GEWA-B, PB, and Turbo-B/E tubes have been optimized for bulk boiling of refrigerants and similar fluids. Coupled with ideally matched surfaces on the inside of the tubes, optimum heat transfer coefficients can be achieved. GEWA and TURBO Evaporator Tubes are available with outer and inner surfaces adapted for specific needs of your application.
GEWA
- B5 & B6 – For highest performance and efficiency
- B4HSL – For weight optimized alternatives as a "drop-in" solution
- BHV – For media with high viscosities
- BLF | BPL – For applications with high fouling tendency
TURBO
- B – The original boiling tube
- ESP – Efficient and lightweight
- EHPII – The industry standard boiling tube
- EPT – High efficiency in ferrous alloys
Our Materials
We offer you a broad portfolio of materials and can expand our offerings at any time to meet your specific needs regarding thermal conductivity, mechanical properties, or corrosion resistance. Enhanced surface tubes made by Wieland Thermal Solutions are already available in copper, copper-nickel, brass, carbon steel, stainless steel, and titanium.

You can find more product information here
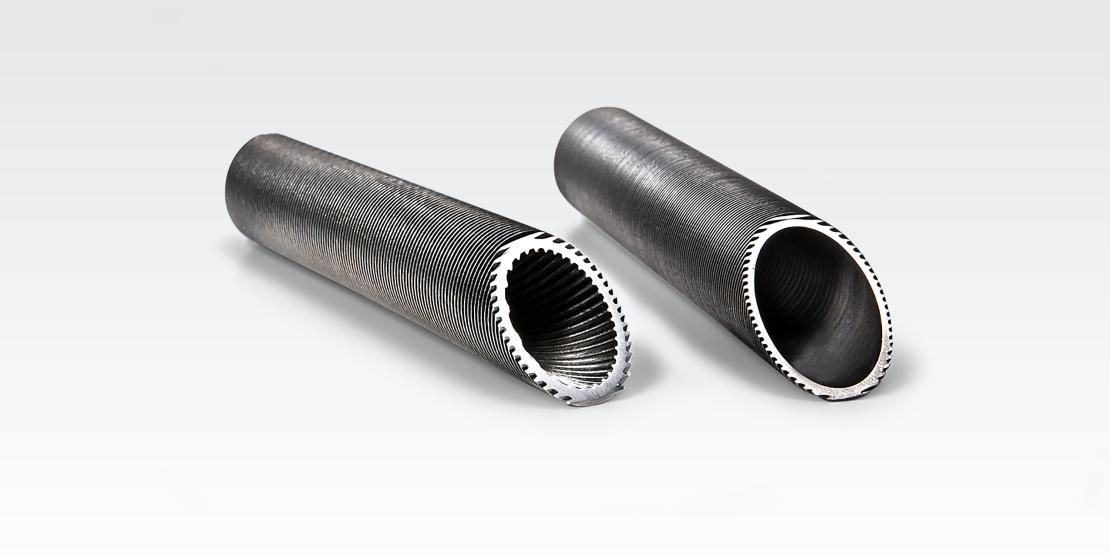
For extreme efficiency in a variety of applications
Low-finned tubes are a reliable solution for controlling the temperature of gases and liquids, or for evaporating and condensing refrigerants. Thanks to their larger heat transfer surface area, they offer considerable potential to save in terms of materials and fill volumes. The wide range of dimensions offered by Wieland Thermal Solutions makes these products perfect for a broad scope of applications in the refrigeration and air conditioning industry, for oil/gas coolers in machinery and plant engineering, and for intermediate vapor superheaters in process engineering.
Your advantages at a glance
- Proven solution in a wide range of applications
- Increased heat transfer surface compared to plain tubes
- Material savings due to reduced tube length
- Filling quantity reduction due to higher efficiency
Materials
GEWA-K tubes offer a greater outer surface area compared to plain tubes. This is ideal for scenarios where the heat transfer surface coefficients vary significantly between the shell tube and the inner tube.
In GEWA-KS tubes, a special pattern is formed on the inside of the tube. This is ideal for scenarios with a low-heat transfer coefficient on the tube side, or an equally low-heat transfer coefficient on both sides.
Our Materials
We offer you a broad portfolio of materials and can expand our offering at any time to meet your specific needs regarding thermal conductivity, mechanical properties, or corrosion resistance. Low-finned tubes made by Wieland Thermal Solutions are already available in copper, copper-nickel, brass, carbon steel, stainless steel, and titanium.

You can find more product information here
GEWA-K/KS
S/T Trufin & TurboChil in Steel
S/T Trufin & TurboChil in Titanium
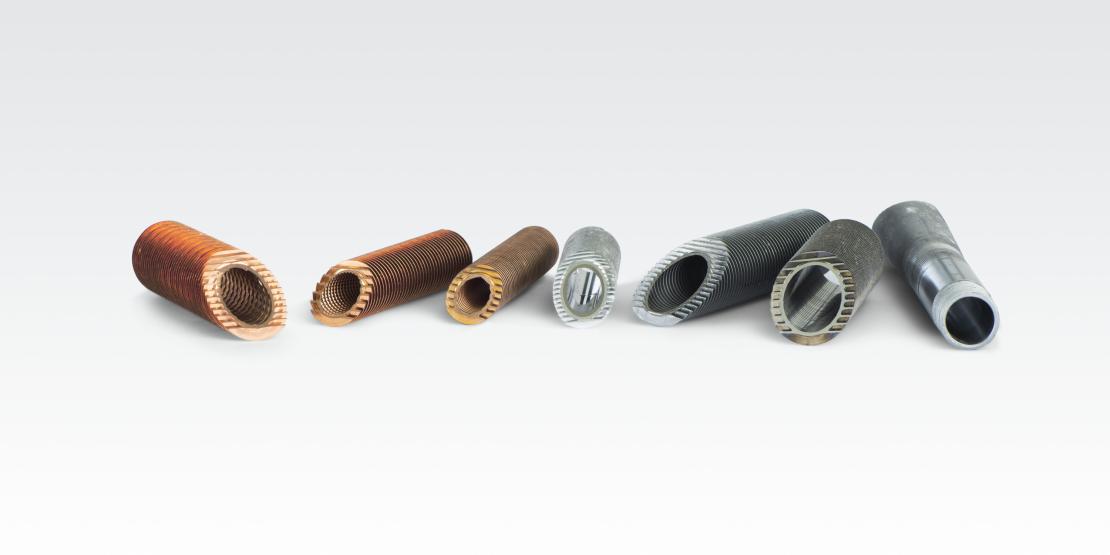
For compact coils and bent shapes
Medium-high finned tubes feature a significantly larger heat transfer surface area compared to plain tubes. They are ideal for compact and high-performance coils and shell-and-tube heat exchangers. Wieland medium-high finned tubes are a proven and robust solution for water heaters, storage tanks, refrigerant condensers, oil coolers, gas coolers or safety heat exchangers and more.
Your advantages at a glance
- High surface enlargement compared to plain tubes
- Ideal for compact and robust heat exchangers
- Excellent bending properties and processability
- Availability of various dimensions, internal structures and materials
Materials
GEWA-D finned tubes made of copper and copper alloys are available in a wide range of sizes and withstand the highest mechanical and thermic stress. They are specially made for the individual geometries of complex heat exchangers. Copper offers the highest heat conductivity of all technical metals. It is superior in processing, hygienic and a corrosion resistant solution.
GEWA-D finned tubes made of aluminium are specifically used in light-weight applications. Aluminium combines highest ductility with reasonable heat conductivity.
GEWA-D finned tubes made of carbon steel can be used in applications such as solid-fuel boilers or storage tanks. The significantly enlarged surface area compared to plain tubes allows compact solutions. Ready to install heat exchangers can be an interesting alternative solution for heat exchangers made of costly materials.
GEWA-D medium-high finned tubes made of stainless steel can be used for condensing boilers or domestic hot water applications. Due to the enlarged outside heat transfer surface area the required tube length can be reduced and thus costly material can be saved.
Our Materials
We offer the widest range of material in the industry and can extend it on request in case of special requirements for heat conductivity, mechanical properties or corrosion resistance. Medium-high finned tubes from Wieland Thermal Solutions are available in copper, copper-nickel, aluminium and carbon steel as well as in stainless steel in limited range.

You can find more information here
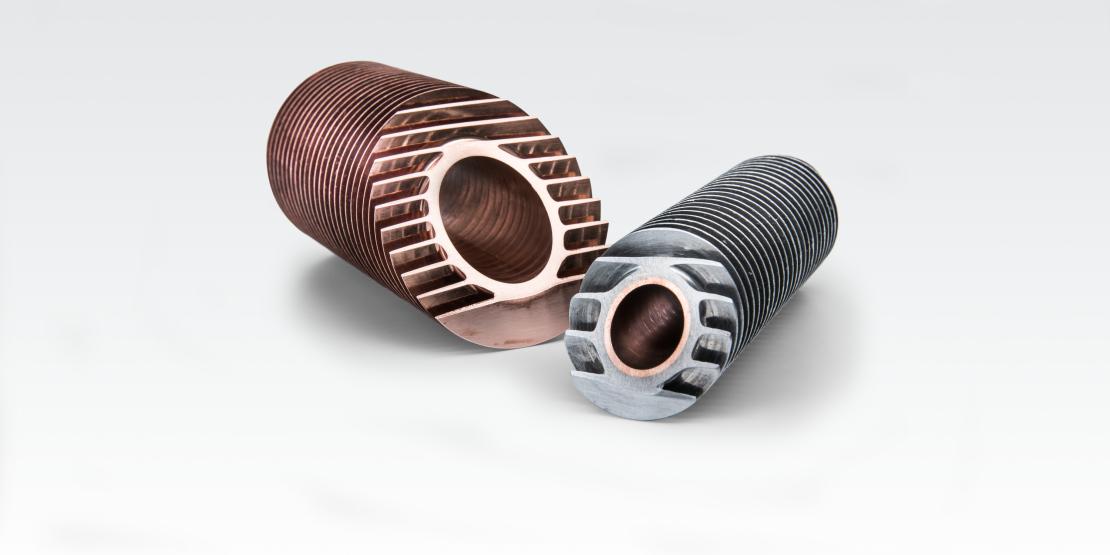
For highest efficiency in controlling the temperature of gases and liquids
High-finned tubes have a much greater outer surface area than smooth tubes. This allows for particularly compact designs. Thanks to their high, thin fins, these tubes perform particularly well in the heating and cooling of liquids and gases, making them an excellent choice for applications in heating technology, as well as in machinery and plant engineering.
Your advantages at a glance
- Highest surface enlargement compared to plain tubes (up to factor 18)
- Enables particularly compact and robust designs
- Available in straight lengths or as coiled heat exchanger
- Also available as bimetallic version GEWA-HB
Materials
GEWA-H tubes are available in a wide variety of sizes, either in straight sections or as coiled heat exchangers. They are primarily used as heat exchangers in gas boilers and as oil and gas coolers in applications related to machinery and plant engineering.
GEWA-HB tubes are high-finned tubes with a fixed inner tube made of a different material. This allows for more corrosion resistant (premium) materials to be used in combination with other, less expensive materials.
Our Materials
We offer you a broad portfolio of materials and can expand our offering at any time to meet your specific needs regarding thermal conductivity, mechanical properties, or corrosion resistance. High-finned GEWA-H tubes made by Wieland Thermal Solutions are already available in copper, copper-nickel and aluminum.
In the GEWA-HB tube materials like carbon steel, stainless steel, titanium or almost any other material like brass and nickel can be used for the inner tube.

You can find more information here
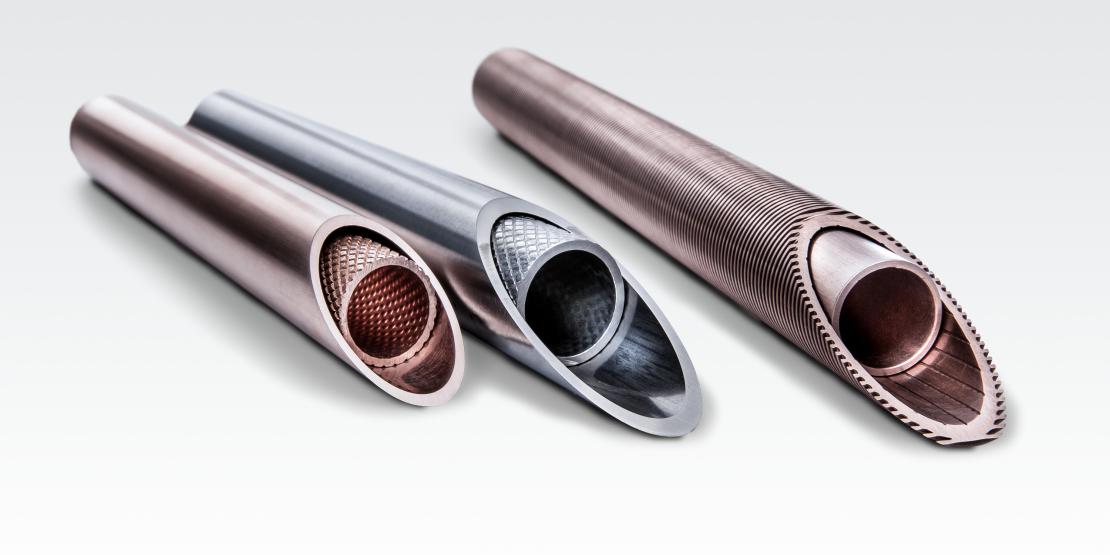
For absolutely reliable media separation with best thermal contact
Safety tubes are used for economical and safe heat transfer. The double wall tubes feature defined leakage paths for the absolutely reliable separation of fluids. For your individual requirements concerning fluid dynamics, we decide on the most suitable surface structure. Our GEWA-safe tubes are a reliable and safe choice for applications such as the direct heating of drinking water using critical fluids as in heating technology or for controlling the temperature of sensitive chemical processes.
GEWA-safe tubes are available in copper and copper alloys and provide safe drinking water heating in heat pumps, heat recovery systems, heat transfer stations and are used for transformer cooling.
Your advantages at a glance
- Reliable | Trust in reliable media separation through the double-tube system with defined leakage spaces.
- Efficient | Use direct and safe heat transfer of the media involved.
- Highest system availability | Detect leaks at an early stage and eliminate them during scheduled maintenance.
- Compact and economical | Reduce material costs and equipment requirements.
Our Materials
We offer you a broad portfolio of materials and can expand our offering at any time to meet your specific needs regarding thermal conductivity, mechanical properties, or corrosion resistance. GEWA-safe double wall tubes are available in copper and copper-nickel.

Read more
Heat exchanger for direct condensation in domestic hot water
Heat recovery from grey water
You can find more information here
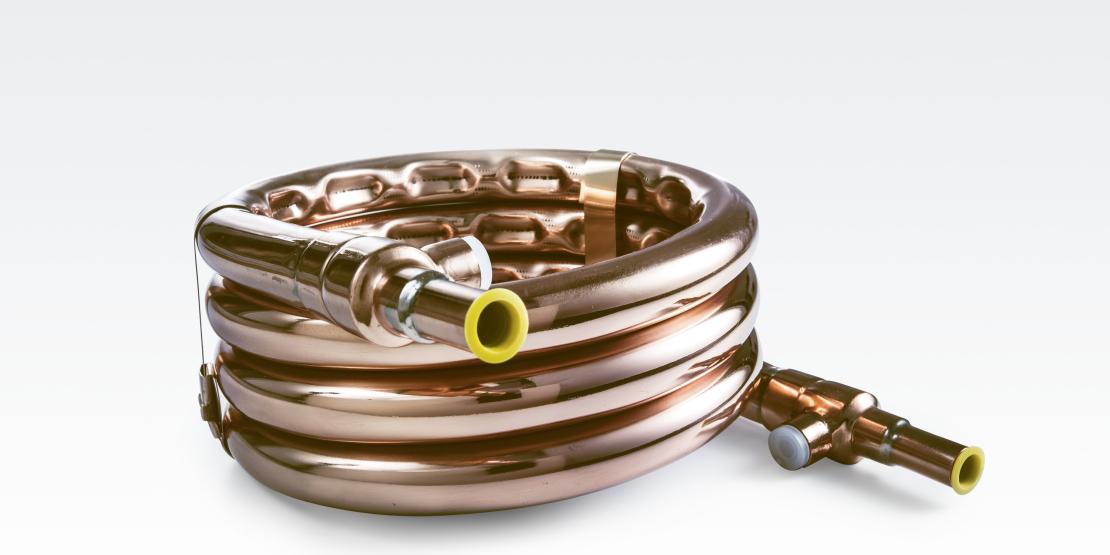
In coaxial heat exchangers, fluids are ideally conducted in counter-flow directions. The Wieland WKE and WKC series have been optimized for the condensation or evaporation of refrigerants and are used in reciprocating chillers and heat pumps.
Your advantages at a glance
- High specific power due to optimized inner tubes
- Flow guidance in counterflow
- Insensitive to frost
- Low fouling tendency
- Long service life
- Reversible operation possible
- Standard designs from stock
You can find more information here
Data sheet WKC | WKE
Our wholesaler for standard heat exchanger
Calculate your coaxial heat exchanger directly online:
ThermalS
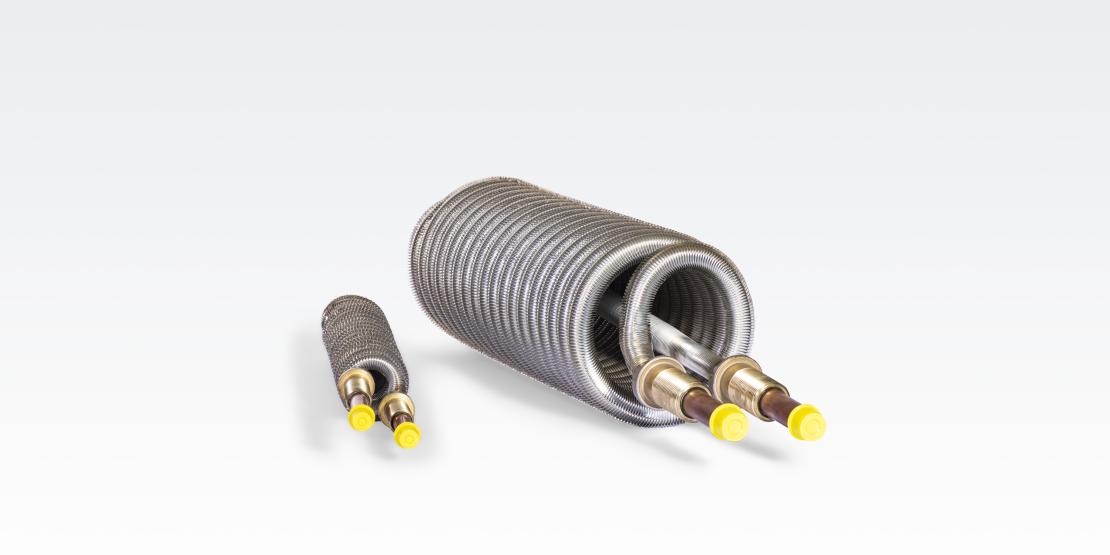
WRK finned tube heat exchangers are suitable for efficient direct condensation and evaporation in heat pump buffer tanks. The inner grooved surface of the used finned tubes optimize the heat transfer. Thus highest COP-values are possible even with smallest temperature differences.
Your advantages at a glance
- Efficient: Highest COP values due to direct integration of the heat exchanger in the storage tank
- Filling volume optimized: Smallest refrigerant volumes due to compact design
- Easy handling: Easy replacement and maintenance
You can find more information here
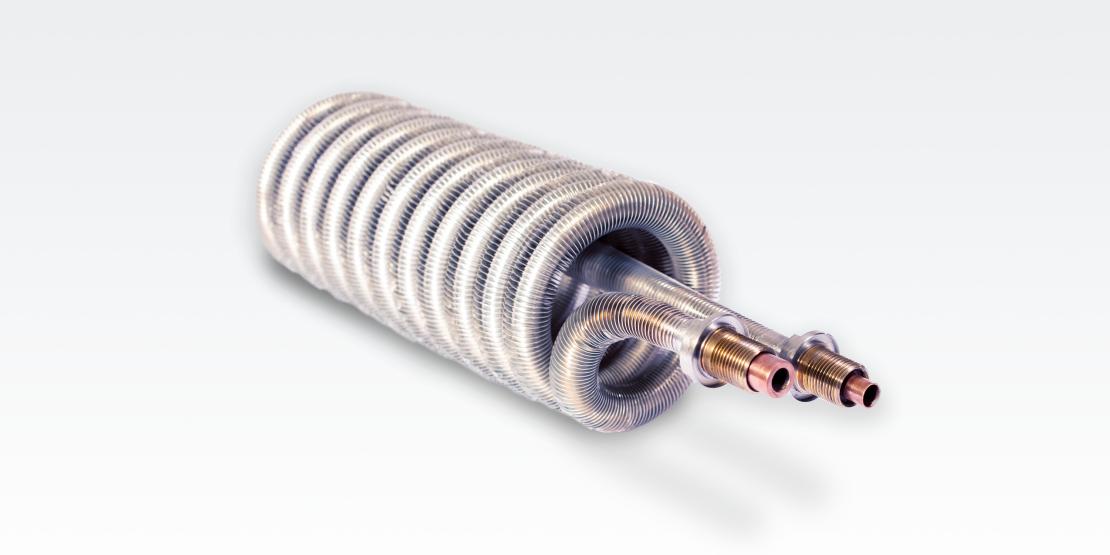
Hygienic and compact: Wieland Safety Heat Exchangers are ideal for the direct heating of water for domestic use by condensing the refrigerant within the tank. The double-walled model offers additional safety against contamination and complies with the guidelines for ensuring the quality of drinking water.
4 good reasons for the Wieland safety heat exchanger series
- Cost-effective | Benefit from higher performance with the lowest refrigerant and material consumption!
- Efficient | Achieve the highest COP values according to DIN EN 16147 by installing the heat exchanger directly in the storage tank.
- Safe | Rely on absolutely reliable media separation through double tubes
- Easy handling | Reduce your effort for installation and replacement.
You can find more information here
More about direct condensation in the storage tank
Data sheet Safety Heat Exchanger
Our wholesaler for standard heat exchanger
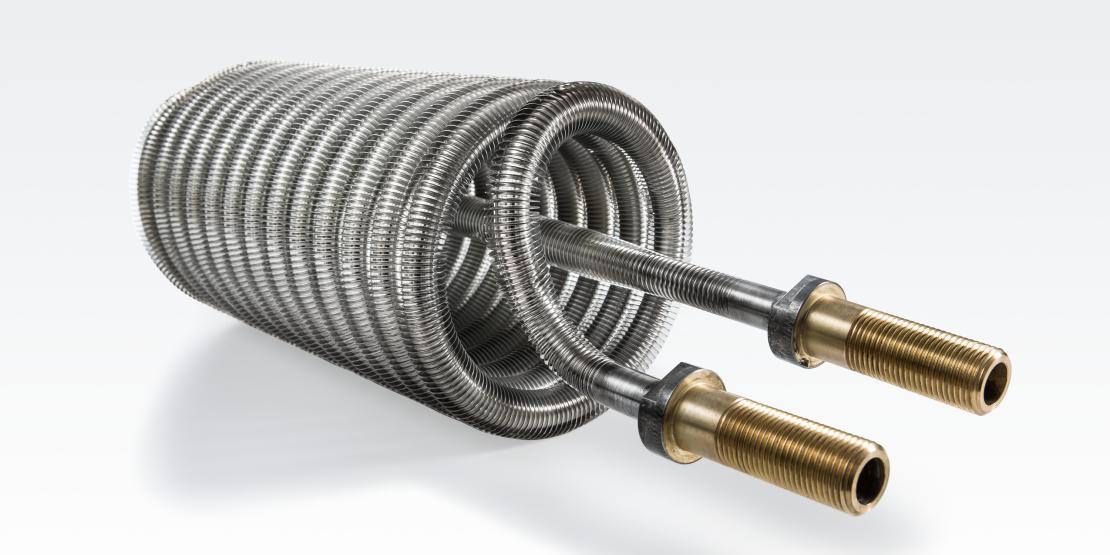
Storage heating, circulation heating of domestic water, protecting solid fuel boilers from overheating, or controlling the temperature of oils and emulsions: With our WRW series of heat exchangers, you are putting your trust in highly developed, compact solutions that are ready to install.
Your advantages at a glance
- Compact design due to high thermal conductivity of copper combined with increased heat transfer area
- Proven corrosion resistance
- Retrofittable due to compact spiral design
- Standard designs from stock
You can find more information here
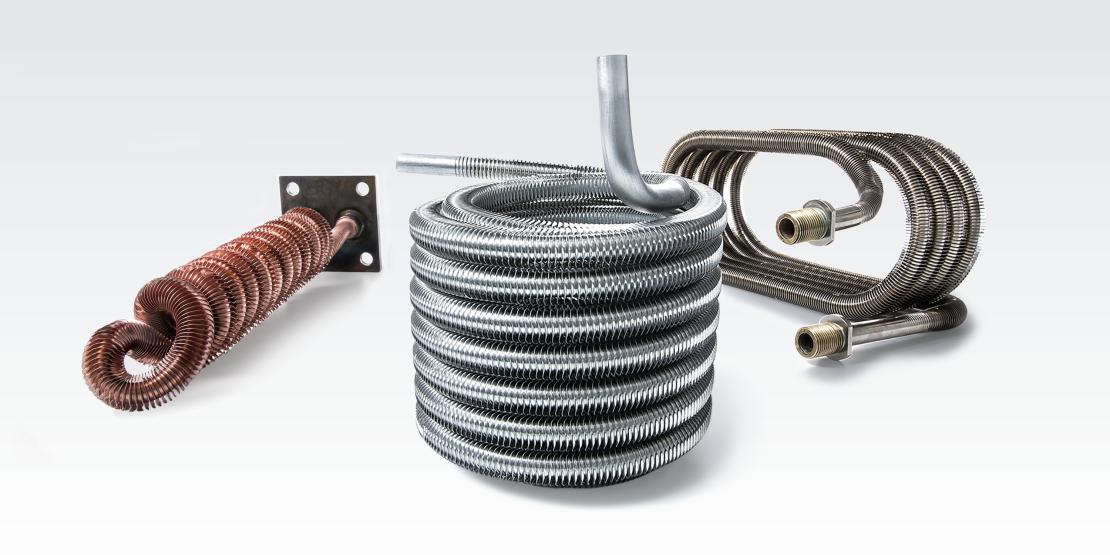
Figure out with us the best heat exchanger design for your heat-transfer challenge
The requirements of heat exchangers are as diverse as their applications - this is why nine out of ten heat exchangers we deliver, are customized to our clients' needs. Together with you, we develop innovative heat exchanger concepts that clearly set you apart from other manufacturers in terms of efficiency, compact design and service life: from customized fittings for optimum installation through to the complete heat exchanger design in the material that best suits your application. For challenging operations like the use of natural refrigerants, e.g. in transcritical CO2 systems (R744) with high operating pressures up to 130 bar, or for applications with propane (R290), ammonia (R717) and water (R718), we serve you with our knowledge from the very beginning of your design.
Our offer
- Together we clarify your heat-transfer and design challenge,
- we design the best solution using our CAD heat-transfer and forming technology know-how,
- we create functional prototypes and
- measure their performance at our in-house thermal engineering laboratory,
- supporting you from the design of the prototype through to series production.
Your application
We are delivering customized solutions to fulfill your requirements – less refrigerant volume and material usage, a very compact design for your special construction space or higher safety aspects. With this flexibility we are well prepared for your special applications, for example the use of natural high pressure refrigerants or the advancement of an ambitious laser gas cooling.
Your benefits at a glance
- Solution for your specific heat-transfer challenge
- Compact solutions using as little material as possible
- Ready-to-install solutions for your trouble-free series production
- Optimal thermal characteristics at low pressure drops
- Engineering and manufacturing from a single source
Our materials
Depending on your requirements regarding corrosion resistance, thermal conductivity as well as mechanical and processing properties, we choose the most suitable material.

You can find more product information here
Customized Heat Exchangers
Safety heat exchanger for domestic hot water heat pump
Design your S&T heat exchangers directly online:
ThermalS
Materials
Wieland | EN Designation | EN No. | ASTM UNS-No. |
---|---|---|---|
K08 | Cu-OFE | CW009A | C10100 |
K12 | Cu-HCP | CW021A | C10300 |
K18/K32 | Cu-ETP | CW004A | C11000 |
K20/K21/K28 | Cu-DHP | CW024A | C12200 |
K30 | Cu-OF | CW008A | C10200 |
Wieland | EN Designation | EN No. | ASTM UNS-No. |
---|---|---|---|
K41 | CuNi1Pb1P* | - | C19150 / C19160 |
K52 | CuNi2Si | CW111C | C70260 |
K53 | CuNi2SiS* | - | - |
K54 | CuNi2SiCr* | - | C81540 |
K60 | CuCr1Zr | CW106C | C18150 |
K61 | CuCr1Zr | CW106C | C18200 |
K65 | CuFe2P | CW107C | C19400 |
K81 | CuSn0,15 | CW117C | C14415 |
KC1 | CuPb1P | CW113C | C18700 |
eco KS2® | CuSP | CW114C | C14700 |
Wieland | EN Designation | EN No. | ASTM UNS-No. | JIS-No. |
---|---|---|---|---|
Z11 | CuZn35Pb1 | CW600N | C34000 | |
Z12 | CuZn35Pb2 | CW601N | C34200 / C34500 | |
Z14 | CuZn37Pb2 | CW606N | C35300 | |
Z21 | CuZn38Pb2 | CW608N | C3713 | |
Z23 | CuZn36Pb3 | CW603N | C36000 | |
Z29 | CuZn39Pb2 | CW612N | C37700 | |
Z31/Z41/Z48 | CuZn40Pb2 | CW617N | C38000 | |
Z32/Z33 | CuZn39Pb3 | CW614N | C38500 | |
Z40 | CuZn43Pb2Al | CW624N | - | |
Z43 | CuZn33Pb1AlSiAs | CW725R | - | |
Z45/Z46 | CuZn36Pb2As | CW602N | C35330 |
Wieland | EN Designation | EN No. | ASTM UNS-No. |
---|---|---|---|
L10/L13/L15 | CuNi10Fe1Mn | CW352H | C70600 |
L30 | CuNi30Mn1Fe | CW354H | C71500 |
Wieland | EN Designation | EN No. | ASTM UNS-No. | JIS-No. |
---|---|---|---|---|
M10 | CuZn10 | CW501L | C22000 | C2200 |
M15/M16/M17 | CuZn15 | CW502L | C23000 | |
M20 | CuZn20 | CW503L | C24000 | C2400 |
M30/M34 | CuZn30 | CW505L | C26000 | C2600 |
M36 | CuZn36 | CW507L | C26800 / C27000 | C2700 |
M37/M38 | CuZn37 | CW508L | C27200 | C2720 |
eco M41® | CuZn38As | CW511L | C27453 | |
eco M57® | CuZn42 | CW510L | - | |
eco M58® | CuZn42 | CW510L | - |
Wieland | EN Designation | EN No. | ASTM UNS-No. |
---|---|---|---|
S40 | CuZn37Mn3Al2PbSi | CW713R | C67420 |
eco S34® | CuZn34Mn2SiAlNi* | - | C67340 |
eco SW1® | CuZn21Si3P | CW724R | C69300 |
eco SW5® | CuZn21Si3P | CW724R | C69300 |
eco SZ2® | CuZn36Si1P | CW726R | C68370 |
eco SZ3® | CuZn40SiP | - | - |
eco SZ4® | CuZn42 | CW510L | C28500 |
eco SZ5® | CuZn40 | CW509L | C27450 |
ecobrass SW4 | CuZn21Si3P | CW724R | C69305 |
Wieland | EN Designation | EN No. | ASTM UNS-No. |
---|---|---|---|
B06 | CuSn6 | CW452K | C51900 |
B09/B10 | CuSn8 | CW453K | C52100 |
B12/B21 | CuSn8P/CuSn8 | CW459K/CW453K | C52100 |
B44/B45 | CuSn4Pb4Zn4 | CW456K | C54400 |
BV9 | CuSn6 | CW452K | C51900 |
eco BS4® | CuSn5NiPS* | - | - |
Wieland | EN Designation | EN No. | ASTM UNS-No. |
---|---|---|---|
U35 | CuAl10Ni5Fe4 | CW307G | C63020 |
U36 | CuAl11Fe6Ni6 | CW308G | - |
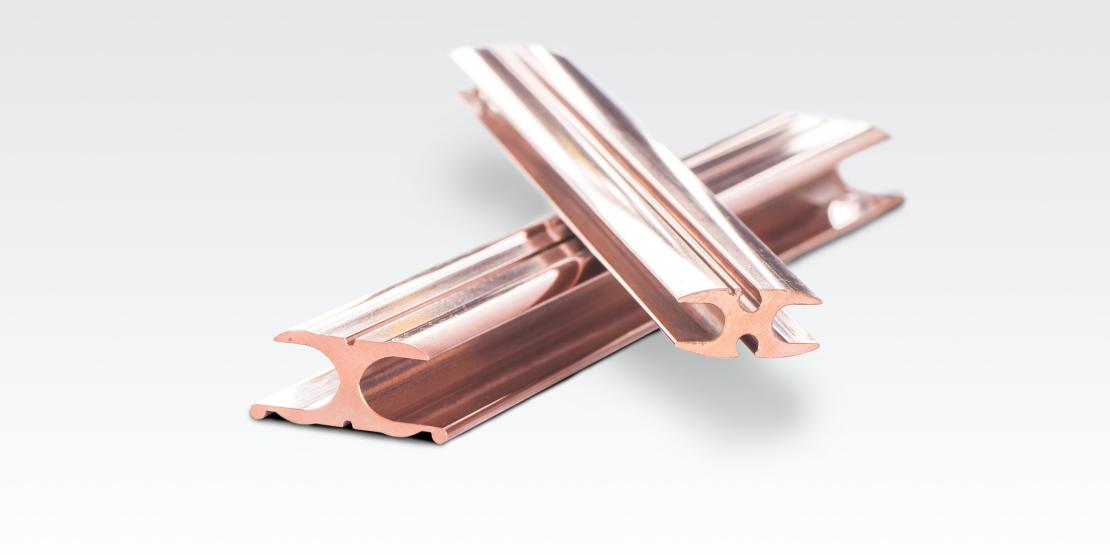
Wieland | EN Designation | EN No. | ASTM UNS-No. |
---|---|---|---|
K12 | Cu-HCP | CW021A | C10300 |
K16 | Cu-ETP1 | CW003A | - |
K18/K32 | Cu-ETP | CW004A | C11000 |
K20/K21/K28 | Cu-DHP | CW024A | C12200 |
K30 | Cu-OF | CW008A | C10200 |
KA1 | CuAg0,10P | CW016A | - |
Wieland | EN Designation | EN No. | ASTM UNS-No. |
---|---|---|---|
N22 | CuNi12Zn24 | CW403J | C75700 |
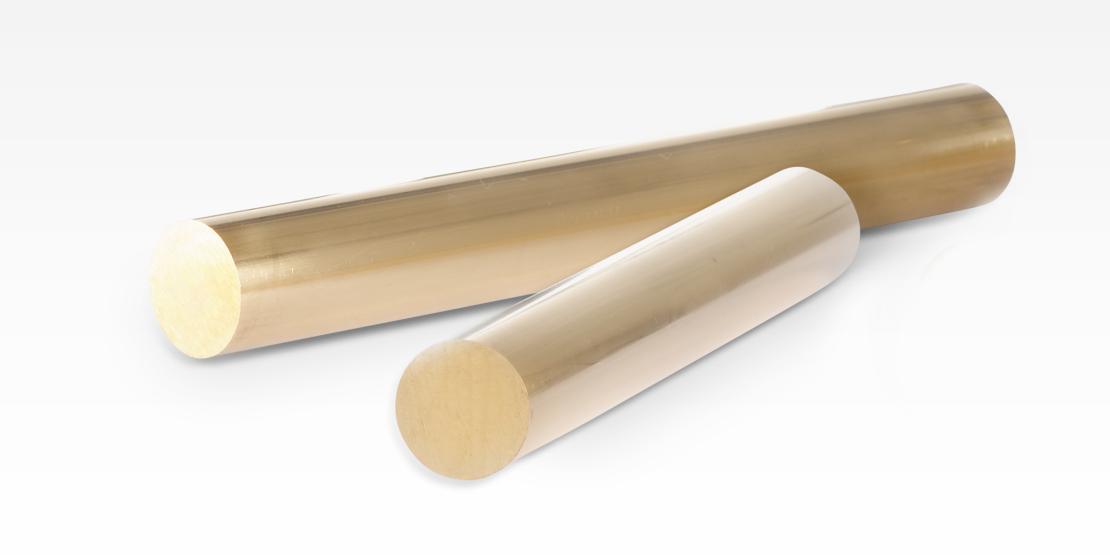
Our W5000 round rods are our premium product for your high performance machining operations. We guarantee the minimum diameter variance in the one batch and a straightness of 0.55 mm/m up to a diameter of 80 millimetres. And best of all: tight alloying tolerances for consistent machining results. Fine, uniform lead distribution for top machinability. Low contamination levels and optimised phase distribution for long tool lives.
Learn more
W5000 precision brass rods
The closer the input stock approaches the end product, the higher the efficiency of downstream machining. The Wieland E5006 precision hexagon rod fulfils these expectations in a quite special way: It presents the precise outer contours of a workpiece. Unlike machined multiedge cross sections, drawn edged rods are characterised by extremely smooth, plane, and compacted surfaces. Moreover, they lend the workpiece a continuous grain structure of high impact toughness. Obvious material savings are yet another benefit.
Learn more
W5006 precision brass rods
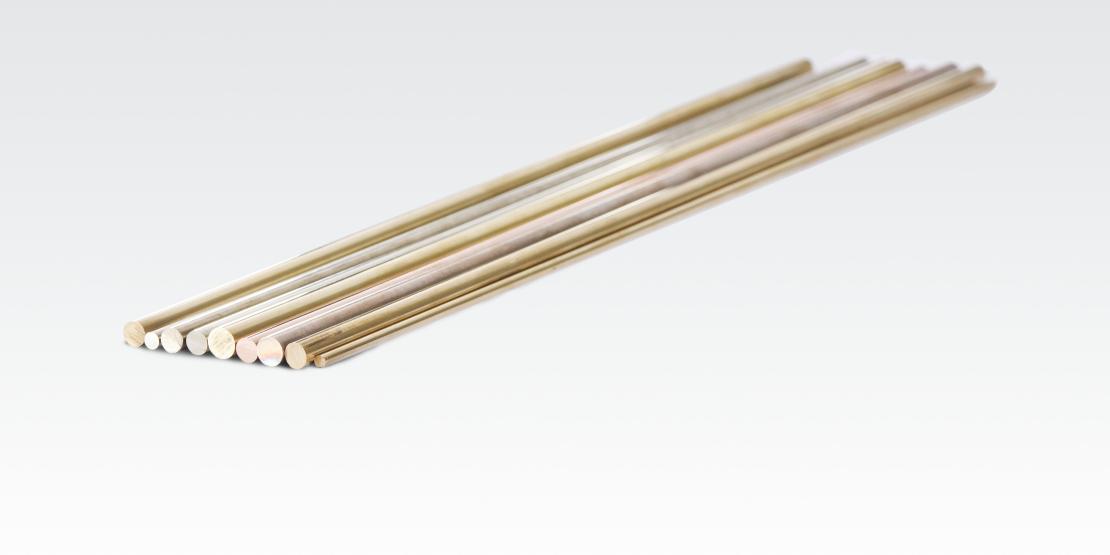
The Wieland WICONNEC brand offers a range of copper materials in the form of rods and wires that are ideal for machined sockets and pins for plug connectors. This material portfolio also offers brass materials in addition to specially developed copper alloys for complex turned plug connectors.
Materials
Wieland | EN Designation | EN No. | ASTM UNS-No. |
---|---|---|---|
K41 | CuNi1Pb1P* | - | C19150 / C19160 |
K44 | CuNi1Pb0.6P* | - | C19140 / C19150 |
KC1 | CuPb1P | CW113C | C18700 |
eco KS2® | CuSP | CW114C | C14700 |
Wieland | EN Designation | EN No. | ASTM UNS-No. |
---|---|---|---|
K55 | CuNi3Si1Mg* | - | C70250 |
Wieland | EN Designation | EN No. | ASTM UNS-No. | JIS-No. |
---|---|---|---|---|
Z10 | CuZn37Pb0,5 | CW604N | C33500 | |
Z11 | CuZn35Pb1 | CW600N | C34000 | |
Z12 | CuZn35Pb2 | CW601N | C34200 / C34500 | |
Z14 | CuZn37Pb2 | CW606N | C35300 | |
Z21 | CuZn38Pb2 | CW608N | C3713 | |
Z23 | CuZn36Pb3 | CW603N | C36000 | |
Z32/Z33 | CuZn39Pb3 | CW614N | C38500 |
Wieland | EN Designation | EN No. | ASTM UNS-No. |
---|---|---|---|
eco S34® | CuZn34Mn2SiAlNi* | - | C67340 |
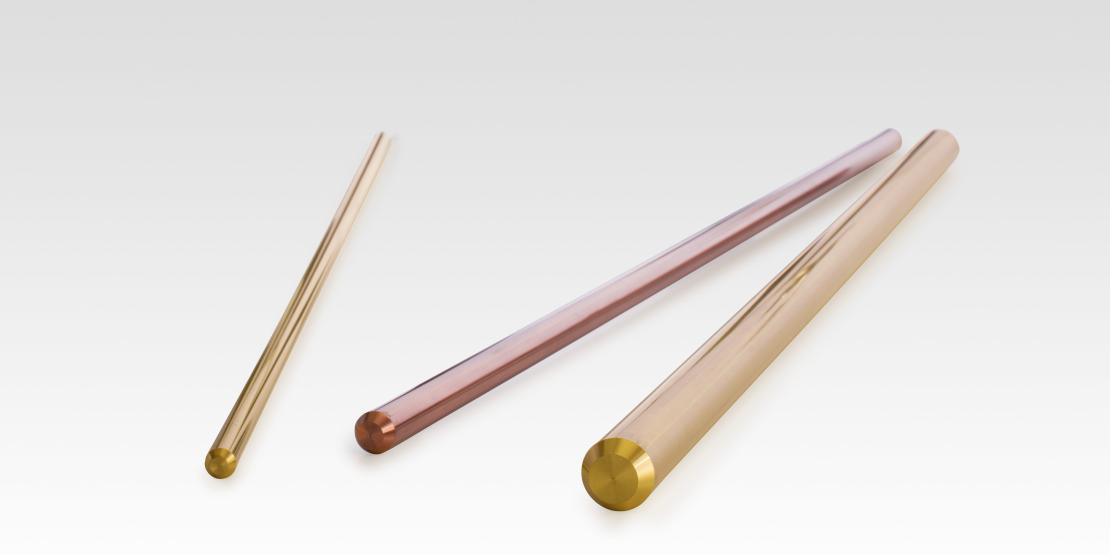
Learn more about
Wieland ecoline
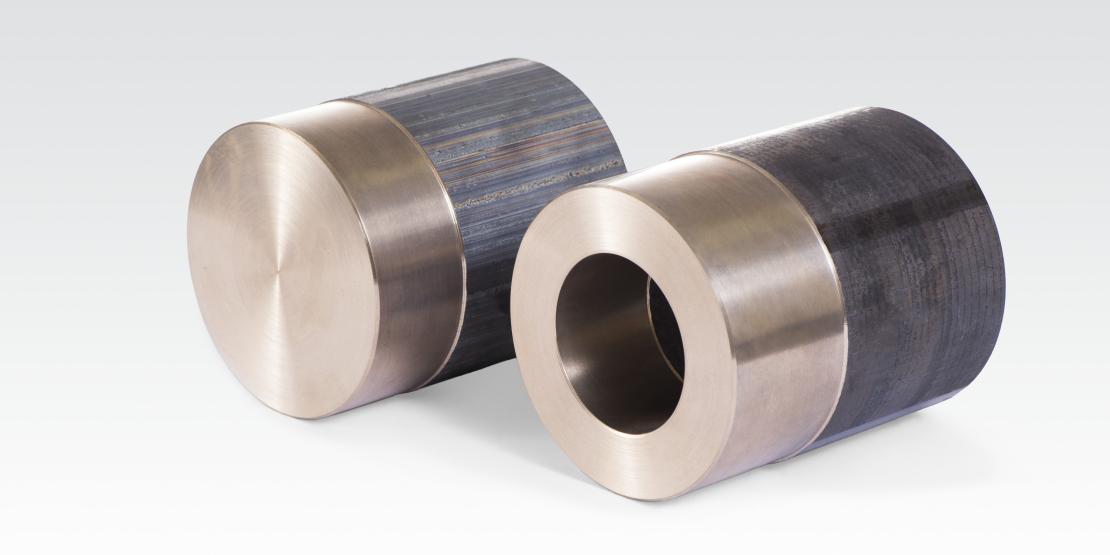
From Europe’s largest copper alloy foundry in Vöhringen/Iller (Germany), we can offer you far in excess of a hundred different copper materials. These include not only a wide range of continuous castings like tubes and rods, but also shaped rods and sections of complex geometries. At the same time, our flexibility ensures the prompt realisation of your special custom wishes.
Materials
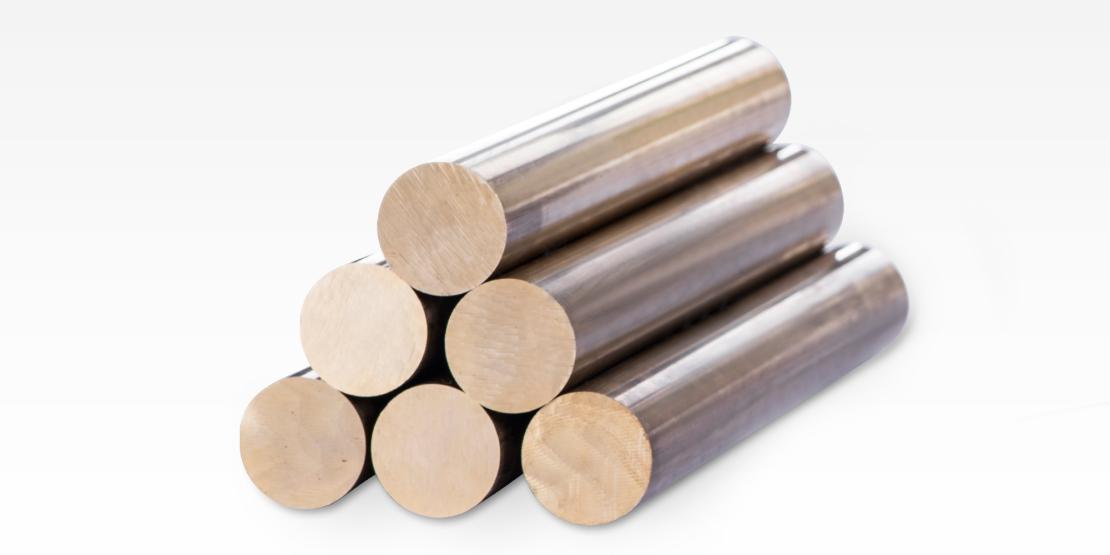
Wieland hot stamping rods
Good forging results can be obtained only when all links in the process chain have been matched to each other to the optimal effect. With Wieland hot stamping rods you are offered a forging stock which comprehensively fulfils these requirements. Your benefits: uniform dark surface for reproducible processing properties, tight diameter tolerances in the drawn size range, and hence precise configuration of the slug weight.
Materials
Wieland | EN Designation | EN No. | ASTM UNS-No. |
---|---|---|---|
eco SW1® | CuZn21Si3P | CW724R | C69300 |
ecobrass SW4 | CuZn21Si3P | CW724R | C69305 |
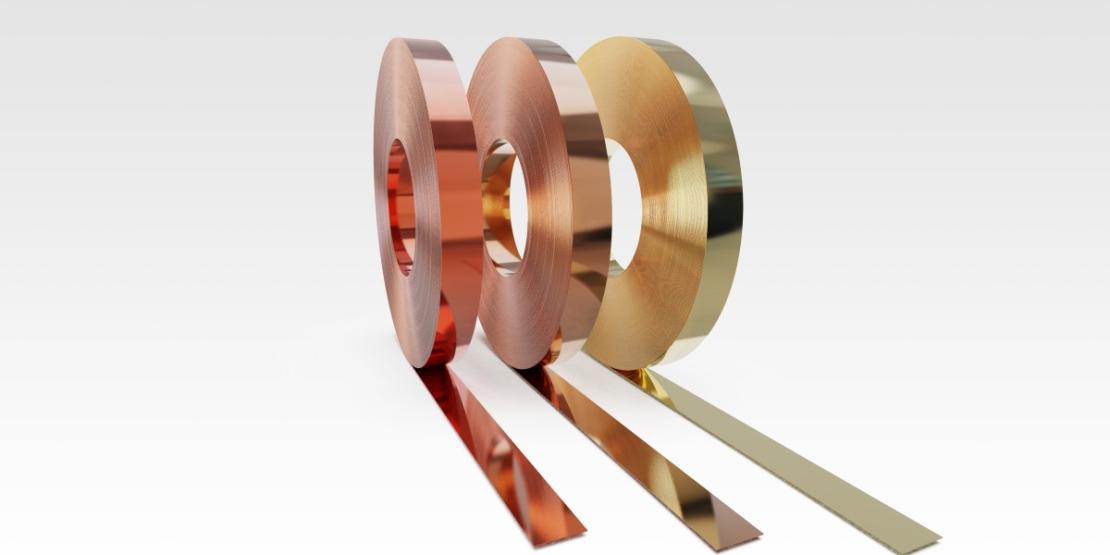
Learn more
Strips for connector
Hot dip tinned copper and copper-alloy strip
Strip for semiconductor packages
Materials
Wieland | EN Designation | EN No. | ASTM UNS-No. | JIS-No. |
---|---|---|---|---|
K09 | Cu-OFE | CW009A | C10100 | C1011 |
K11 | Cu-OF | CW008A | C10200 | |
K12 | Cu-HCP | CW021A | C10300 | |
K14 | Cu-PHC | CW020A | C10300 | |
K19 | Cu-DHP | CW024A | C12200 | C1220 |
K32 | Cu-ETP | CW004A | C11000 | C1100 |
Wieland | EN Designation | EN No. | ASTM UNS-No. |
---|---|---|---|
K65 | CuFe2P | CW107C | C19400 |
K80 | CuFe0,1P* | - | C19210 |
K81 | CuSn0,15 | CW117C | C14415 |
Wieland | EN Designation | EN No. | ASTM UNS-No. |
---|---|---|---|
K55 | CuNi3Si1Mg* | - | C70250 |
K57 | CuNi1Co1Si* | - | C70350 |
K58 | CuNi3Si1Mg | - | C70250 |
K73 | CuNi1ZnSi* | - | C19005 |
K75 | CuCrSiTi* | - | C18070 |
K76 | CuNiSiP* | - | C19010 |
K82 | - | - | C15100 |
K88 | CuCrAgFeTiSi* | - | C18080 |
Wieland | EN Designation | EN No. | ASTM UNS-No. | JIS-No. |
---|---|---|---|---|
M42 | CuZn42 | CW510L | - | |
M42 | CuZn42 | CW510L | - | |
Z21 | CuZn38Pb2 | CW608N | C3713 | |
Z30 | CuZn39Pb2 | CW612N | C37700 |
Wieland | EN Designation | EN No. | ASTM UNS-No. | JIS-No. |
---|---|---|---|---|
M05 | CuZn5 | CW500L | C21000 | C2100 |
M10 | CuZn10 | CW501L | C22000 | C2200 |
M15 | CuZn15 | CW502L | C23000 | C2300 |
M20 | CuZn20 | CW503L | C24000 | C2400 |
M30 | CuZn30 | CW505L | C26000 | C2600 |
M33 | CuZn33 | CW506L | C26800 | C2680 |
M36 | CuZn36 | CW507L | C26800 / C27000 | C2700 |
M37 | CuZn37 | CW508L | C27200 | C2720 |
M38 | CuZn37 | CW508L | C27200 | C2720 |
Wieland | EN Designation | EN No. | ASTM UNS-No. | JIS-No. |
---|---|---|---|---|
S12 | CuSn3Zn9 | CW454K | C42500 | C4250 |
S23 | CuZn23Al3Co | CW703R | C68800 |
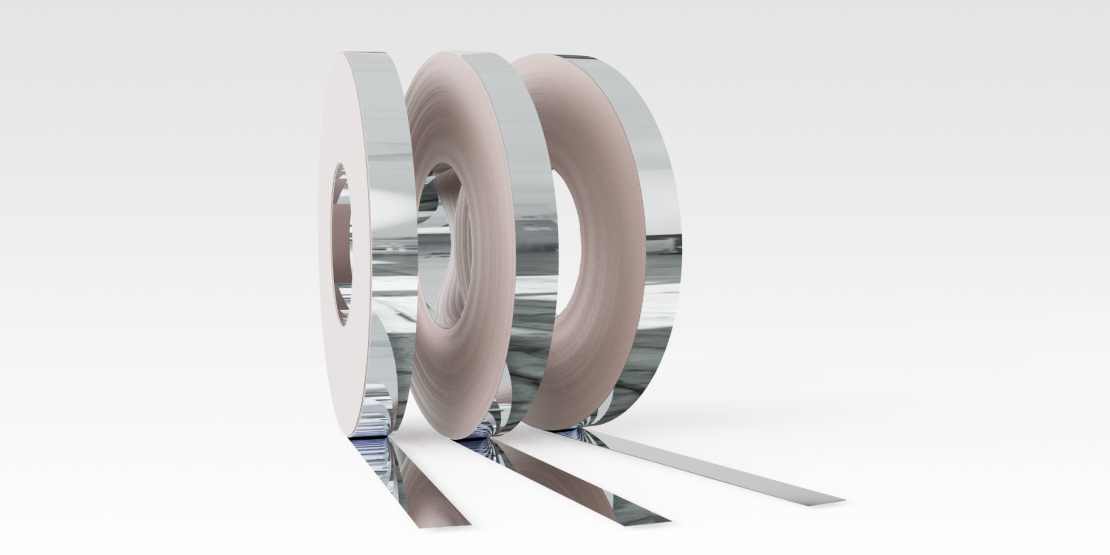
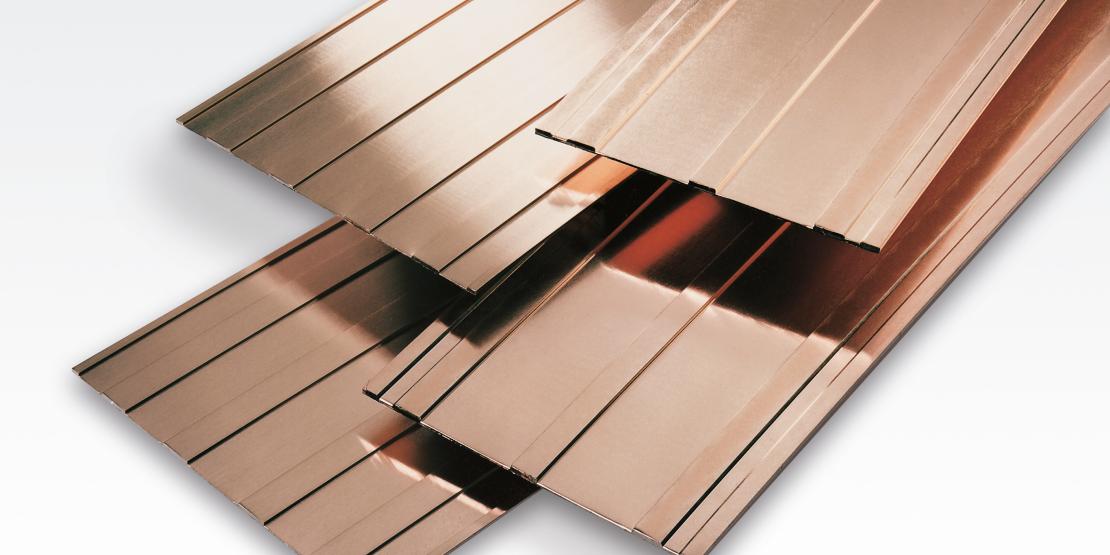
Learn more
Multi-gauge strip
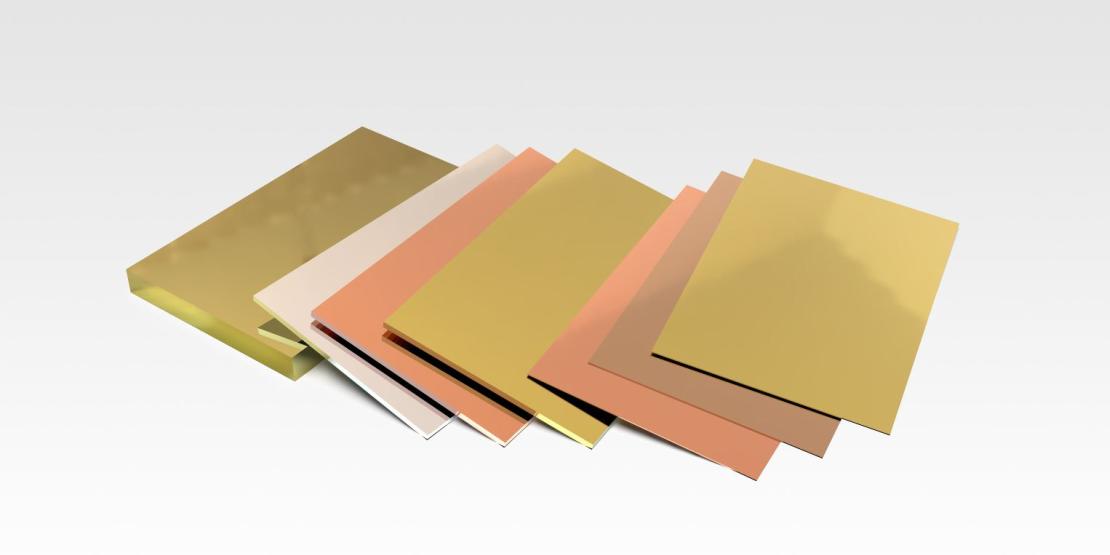
Wieland | EN Designation | EN No. | ASTM UNS-No. |
---|---|---|---|
K55 | CuNi3Si1Mg* | - | C70250 |
K57 | CuNi1Co1Si* | - | C70350 |
K58 | CuNi3Si1Mg | - | C70250 |
K73 | CuNi1ZnSi* | - | C19005 |
K75 | CuCrSiTi* | - | C18070 |
K76 | CuNiSiP* | - | C19010 |
K82 | - | - | C15100 |
K88 | CuCrAgFeTiSi* | - | C18080 |
Wieland | EN Designation | EN No. | ASTM UNS-No. | JIS-No. |
---|---|---|---|---|
M42 | CuZn42 | CW510L | - | |
Z21 | CuZn38Pb2 | CW608N | C3713 | |
Z30 | CuZn39Pb2 | CW612N | C37700 |
Wieland | EN Designation | EN No. | ASTM UNS-No. | JIS-No. |
---|---|---|---|---|
M05 | CuZn5 | CW500L | C21000 | C2100 |
M10 | CuZn10 | CW501L | C22000 | C2200 |
M15 | CuZn15 | CW502L | C23000 | C2300 |
M20 | CuZn20 | CW503L | C24000 | C2400 |
M30 | CuZn30 | CW505L | C26000 | C2600 |
M33 | CuZn33 | CW506L | C26800 | C2680 |
M36 | CuZn36 | CW507L | C26800 / C27000 | C2700 |
M37 | CuZn37 | CW508L | C27200 | C2720 |
M38 | CuZn37 | CW508L | C27200 | C2720 |
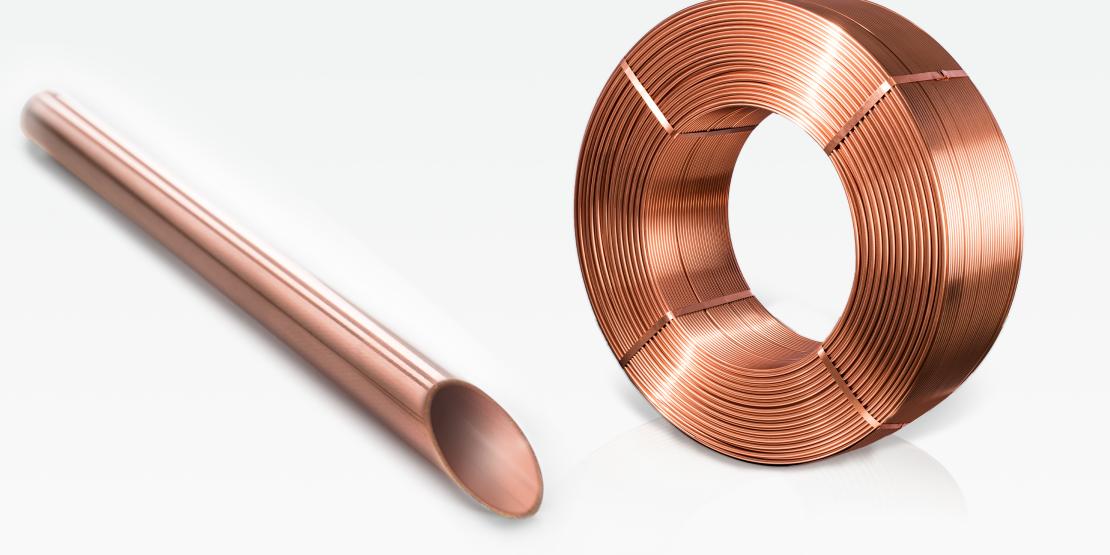
Available materials
Wieland | EN | EN-Nr. | UNS |
K08 | Cu-OFE | CW009A | C10100 |
K12 | Cu-HCP | CW021A | C10300 |
K20 / K21 / K28 | Cu-DHP | CW024A | C12200 |
K30 | Cu-OF | CW008A | C10200 |
K65 | CuFe2P | CW107C | C19400 |
L10 | CuNi10Fe1Mn | CW352H | C70600 |
L30 | CuNi30Mn1Fe | CW354H | C71500 |
Delivery forms
- Level wound coils: 100 kg, 150 kg, 300 kg, 530 kg
- Straight lengths
- Rings
Materials
K65 - Sustainable and efficient
Sustainable and efficient – two keywords that have had a decisive impact on our time and have gained in relevance in recent years, especially in refrigeration. Increased environmental awareness in society and industry has therefore led to a kind of renaissance of natural refrigerants, especially CO2. Wieland supports this turnaround with a tube system that meets the high requirements of CO2 as a refrigerant.
Wieland K65 tubes have been designed for CO2 applications in the commercial field, especially that of supermarket refrigeration systems. Wieland K65 alloy provides the mechanical strength high enough to withstand the high operating pressures of CO2. At the same time, K65 tubes have outstanding processing properties, similar to those of standard copper (Cu-DHP/C12200).
All Wieland K65 tubes are available in the soft condition (R300/O61) to ensure excellent bending / flaring and collaring properties.
Wieland K65 tubes are offered from stock in two pressure ranges, 80 bar and 120 bar, and in dimensions ranging from 3/8” up to 2-1/8”.
Moreover, K65 tubes are also available in individual dimensions and different delivery forms.
For industrial processing, in particular CO2 heat exchanger (evaporator / gas cooler) manufacturing, level wound coils (LWC) are offered.
More K65 products in other categories
Your benefits
- Pressure resistance tailormade to your needs
- Cost reduction through weight reduction
- Proven processing technology: brazing instead of welding!
- Excellent heat transfer
- Design according to EN 14276 - TUEV or UL certification on demand
Typical applications
- Components of R744 refrigeration systems
- Fin coil heat exchangers for higher operation pressures (e.g. R744 evaporators or gas coolers )
- Shell and tube heat exchangers for higher operation pressures (e.g. R744 evaporators or gas coolers)
Technical properties
- Material: K65
- Conditions: soft R300/O61 and hard R420/H80
- Delivery form: Level wound coils or straight lengths
- Coil weights: 100 kg, 150 kg, 300 kg
- Available dimensions: 5 - 28 mm for LWC; 5 - 110 mm for straight lengths
- Usual standards: EN 12735-1 / EN 14276 / ASTM B 1017
Further information
cuproclima
For high-quality seamless inside smooth or innergrooved copper tubes in level-wound coils for the refrigeration and air-conditioning industries. The specified quality and inspection criteria exceed the existing requirements of standards (e. g. EN 12735-2, ASTM).
Your benefits
- longer run time for machines when uncoiling tubes
- reduced scrap for finished products
- reduced set-up time
- detection of even smaller surface defects on the tubes
- possible malfunctions of finished equipment during pressure testing are reduced
- fewer impurities in the refrigerant circuit.
Fields of application
- air-cooled heat exchangers for the air-conditioning and refrigeration industry
- evaporators
- condensers
- heat exchangers
- air coolers
Technical Properties
- Materials Cu-DHP
- Conditions soft and extra soft
- Delivery form level wound coils only
- Coil weights 100 kg, 150 kg, 300 kg
- Available dimensions 4 - 28 mm, wall thicknesses on request
Copper tubes with ultra clean inner surface for industrial applications
Our innovative production process for cuproclean tubes removes carbon film. This results in higher reliability, longer life and reduced maintenance costs.It is suitable for all fresh water applications. Copper offers outstanding versatility and is characterized by excellent formability as well as good processing properties. cuproclean copper tubes are also available in combination with other qualities such as cuproform.
Your benefits
- ultra-clean tube surface free from carbon film
- highest reliability and longer life also in fresh water applications
- best corrosion resistance
- carbon film test according to EN 1057 and confirmation in the certificate
Fields of application
- cooling ceilings
- solar water heating systems
- heat generators
Technical properties
- Materials Cu-DHP
- Conditions Soft
- Delivery form Level wound coils
- Coil weights 100 kg, 150 kg, 300 kg
- Available dimensions 6 - 28 mm, wall thicknesses on request
High formable copper tubes
In boiler manufacture, for example the tubes may be formed by: expanding, bending, upsetting and beading. Industrial copper tubes from conventional production do not always meet these high demands. Therefore, it is often necessary to use additional fittings made from other materials. This results in further production steps and consequently higher production costs.
Your benefits
- no special fittings necessary; this results in lower costs of production
- higher added value in your production
- exceptional forming properties – 80% expansion of the tube end tested and certified on the inspection certificate
- less scrap with very high deformation
Fields of application
- Connecting pieces, e.g. especially for boilers
Technical properties
- Materials Cu-DHP
- Conditions soft and extra soft
- Delivery form Layer-wound coils and straight lengths
- Coil weights 100 kg, 150 kg, 300 kg, 530 kg
- Available dimensions 6 - 28 mm for LWC; 6 - 64 mm for straight lengths
Copper tubes with high-purity outer surface for solar thermal applications
In the process of manufacturing solar heat absorbers requirements vary depending on the application. In the solarclean family you will find the most suitable copper tube quality for your optimized fabrication.
solarclean classic
The particularly clean tube surface ensures a high quality weld. You can therefore save at least one cleaning operation or an extensive pre-treatment of the components to be welded.
solarclean HP
For heat pipes in vacuum tube collectors - highest surface cleanliness on tube outside and inside prevents contamination of the heat transfer medium in the heat pipe and yet ensures the efficiency of the system.
solarclean plus
Improved forming properties for the fabrication of meander-shaped absorber tubes facilitate the setting of the bending machines and increase process reliability. solarclean_plus ensures super clean tube surfaces substantially improving the ultrasonic welding process.
solarclean eco
The cost-effective alternative for laser welding of absorber plate and tubing with sufficient cleanliness.
solarclean SL
Like solarclean classic, solarclean SL ensures superclean tube surfaces. Depending on your fabrication needs, you can also order solarclean in straight lengths.
Technical properties
- Materials Cu-DHP
- Conditions hard, hard relaxed, half-hard
- Delivery form Layer-wound coils and straight lengths
- Coil weights 100 kg, 150 kg, 300 kg, 530 kg
- Available dimensions 6 - 15 mm; wall thicknesses 0.3-1.2 mm
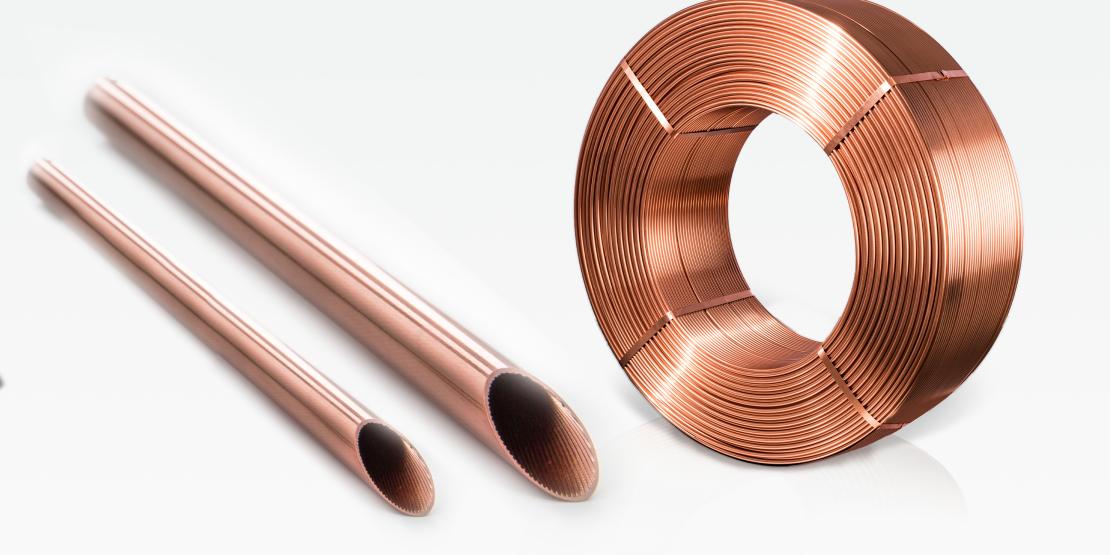
Available materials
Wieland | EN | EN-Nr. | UNS |
K20 / K21 / K28 | Cu-DHP | CW024A | C12200 |
L10 | CuNi10Fe1Mn | CW352H | C70600 |
K65 | CuFe2P | CW107C | C19400 |
Materials
K65 - Sustainable and efficient
two keywords that have had a decisive impact on our time and have gained in relevance in recent years, especially in refrigeration. Increased environmental awareness in society and industry has therefore led to a kind of renaissance of natural refrigerants, especially CO2. Wieland supports this turnaround with a tube system that meets the high requirements of CO2 as a refrigerant.
Wieland K65 tubes have been designed for CO2 applications in the commercial field, especially that of supermarket refrigeration systems. Wieland K65 alloy provides the mechanical strength high enough to withstand the high operating pressures of CO2. At the same time, K65 tubes have outstanding processing properties, similar to those of standard copper (Cu-DHP/C12200).
Innergrooved K65 tubes for manufacturing of CO2 heat exchangers (evaporator / gas cooler) are available in individual dimensions. These are delivered in level wound coils (LWC) or straight lengths alternatively.
Wieland K65 tubes are also available from stock in standard dimensions.
More K65 products in other categories
Your benefits
- Pressure resistance tailormade to your needs
- Cost reduction through weight reduction
- Proven processing technology: brazing instead of welding!
- Excellent heat transfer
- Design according to EN 14276 - TUEV certification on demand
Typical applications
- Fin coil heat exchangers for higher operation pressures (e.g. R744 evaporators or gas coolers)
- Shell and tube heat exchangers for higher operation pressures (e.g. R744 evaporators or gas coolers)
Technical properties
- Materials: K65
- Conditions: soft R300/O61 and hard R420/H80
- Delivery form: Level wound coils or straight lengths
- Coil weights: 100 kg, 150 kg, 300 kg
- Available dimensions: 5 - 16 mm
- Usual standards: EN 12735-1 / EN 14276 / ASTM B 1017
Further information
cuprofin-Standard
Wieland cuprofin-Standard tubes are effiecient heat exchanger tube that are suitable for one and two-phased flow as well as for evaporation and condensation. This enables the flexible production of efficient and compact heat exchangers. There is no need to keep a stock of different specialized tube types.
Your benefits
- improved heat transfer due to fin structure on the inside of the tube
- compact heat exchanger construction
- reduced material input
- Internal structure suitable for evaporation, condensation and single-phase heat transfer
cuprofin-standard is also available in superclean quality and as a microgroove tube.
Fields of application
- Finned heat exchangers for the refrigeration/air conditioning industry
- Evaporator
- Condensers
- Recooler
- Air Cooler
- Tube bundle injection evaporator
- Heat exchangers in the form of coiled elements (e.g. container heating and cooling)
Technical properties
- Delivery form Layer-wound coils and straight lengths up to 7,9m
- Coil weights 100 kg, 150 kg, 300 kg
- Usual standards
- EN 12735-2
- ASTM B359
- VdTÜV 420/6, 420/7
Further Information
cuprofin-C tubes for condensors
Wieland cuprofin-C Tubes are highly efficient heat transfer tubes for the tube-side condensation of refrigerants. Depending on the fluid used, the fins on the inside of the tube are optimized for high performance with low material usage. They enable the design of highly efficient and compact heat exchangers.
Your benefits
- optimized heat transfer due to adapted fin structure on the inside of the tube
- compact heat exchanger construction
- reduced refrigerant charge
- reduced material input
cuprofin-C is also available in superclean quality and as microgroove tube.
Fields of application
- Finned heat exchangers, especially condensers
- Heat exchangers in the form of coiled elements (e.g. container heating)
Technical properties
- Delivery form Layer-wound coils and straight lengths up to 7,9m
- Coil weights 100 kg, 150 kg, 300 kg
- Usual standards
- EN 12735-2
- ASTM B359
- VdTÜV 420/6, 420/7
Further Information
cuprofin-E tubes for evaporators
Wieland cuprofin-E tubes are highly efficient heat transfer tubes for the tube-side evaporation of refrigerants in finned heat exchangers. The fins on the inside of the tubes are designed for optimum performance during flow boiling and the lowest possible pressure drop for a wide range of refrigerants.
Your benefits
- optimized heat transfer due to adapted fin structure on the inside of the tube
- compact heat exchanger construction
- extremely low pressure drop
- reduced material input
cuprofin-E is also available in superclean quality and on requiry as a microgrooved tube.
Fields of application
- Finned heat exchangers, especially evaporators
Technical properties
- Delivery form Layer-wound coils and straight lengths up to 7,9m
- Coil weights 100 kg, 150 kg, 300 kg
- Usual standards
- EN 12735-2
- ASTM B359
- VdTÜV 420/6, 420/7
Further Information
cuprofin-EDX tubes for injection
cuprofin-EDX are highly efficient and stable heat exchanger rubes for Injection evaporator in tube bundle design.
Your benefits
- optimized heat transfer and very low pressure drop
- compact heat exchanger construction
- reduced material input
cuprofin-EDX is also available in superclean quality and on request as a microgroove tube.
Fields of applications
- Tube bundle injection evaporator
Technical properties
- Delivery form Layer-wound coils and straight lengths up to 7,9m
- Coil weights 100 kg, 150 kg, 300 kg, 530 kg
- Usual standards
- EN 12735-2
- ASTM B359
- VdTÜV 420/6, 420/7
Further Information
cuprofin-G tubes for single-phase heat transfer
Wieland cuprofin-G Tubes are highly efficient heat transfer tubes, especially designed for recooling systems and air coolers. The fins on the inside of the tubes are optimized for single-phase heat transfer of aqueous media such as water-glycol mixtures. This enables the production of efficient and compact heat exchangers.
Your benefits
- optimized heat transfer through adapted fin structure on the inside of the tube
- compact heat exchanger construction
- low pressure drop
- reduced material input
cuprofin-G is also available in superclean quality.
Fields of application
- Finned heat exchanger with single-phase heat transfer
- Recooler
- Air cooler
Technical properties
- Delivery form Layer-wound coils and straight lengths up to 7,9m
- Coil weights 100 kg, 150 kg, 300 kg
- Usual standards
- EN 12735-2
- ASTM B359
- VdTÜV 420/6, 420/7
Further Information
cuprofin-L10 tubes for seawater applications
Wieland cuprofin-L10 tubes are efficient heat transfer tubes which are particularly suitable for applications with seawater and other salt water as well as in their surroundings (e.g. coastal areas). The material CuNi10Fe1Mn (Wieland L10) is highly resistant to corrosion and erosion in these fluids. Compared to stainless steels the thermal conductivity of L10 is higher by a factor of approx. 3.
Your benefits
- improved heat transfer due to fin structure on the inside of the tube
- compact heat exchanger construction
- reduced material input
- highly resistant to corrosion and erosion
cuprofin-L10 is also available in superclean quality.
Fields of application
- Finned and bundle tube heat exchangers that are operated with seawater or other saltwater, or installed in coastal areas
Technical properties
- Delivery form Layer-wound coils and straight lengths up to 7,9m
- Coil weights 100 kg, 150 kg, 300 kg
- Usual standards
- EN 12735-2
- ASTM B359.
- VdTÜV 420/6, 420/7
Further Information
microgroove - Small diameter, high performance
With microgroove technology you build your heat exchanger with maximum efficiency and maximum compactness.
Your benefits
- reduced refrigerant charge
- Increased efficiency of the heat exchanger
- compact heat exchanger construction
- reduced material input
- reduced investment costs
microgroove is also available in superclean quality.
Fields of application
- Highly efficient finned heat exchangers
- Evaporator
- Condensers
Technical properties
- Delivery form Layer-wound coils and straight lengths up to 7,9m
- Coil weights 100 kg, 150 kg, 300 kg
- Usual standards
- EN 12735-2
- ASTM B359
- VdTÜV 420/6, 420/7
Further Information
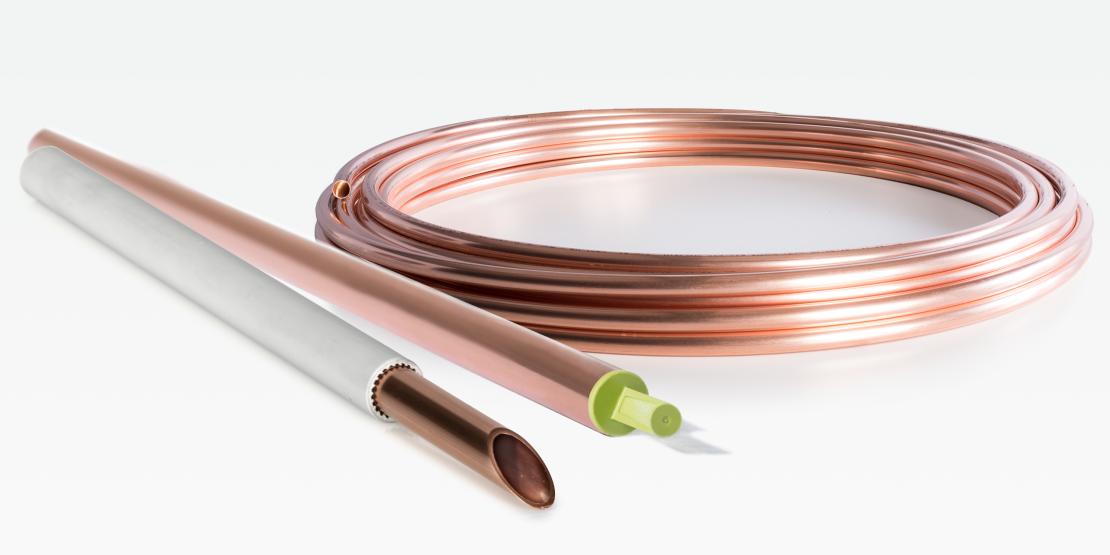
Materials
For a more sustainable future in construction.
With its 100 % share of recycled material, the cuprolife copper tube makes a sustainable difference, and thus makes a significant contribution to the advancement of building and construction as well as building services.
Every cuprolife tube from Wieland is manufactured in keeping with the mass balance approach – using a process with 100 % recycled copper. As the starting point when verifying cuprolife, TÜV SÜD tested the procedure for calculating the 100 % recycled content*.
The new standard in copper tubes: cuprolife®.
Thanks to cutting-edge manufacturing techniques, cuprolife tubes exceed even the highest requirements. Optimal efficiency and reliability are guaranteed along with an exceptional service life. cuprolife tubes are universally usable. cuprolife is permanently in stock and can be supplied in any size from 6 x 1 mm to 159 x 3 mm.
Fields of application
- Domestic hot and cold water supply
- Heating
- Gas
- Liquid gas
- Heating oil / biofuel oil B10
- Solar systems
- Rainwater
- Industrial compressed air
- Sprinkler systems
- Firefighting systems
Technical features
- 100 % recycled copper*
- Design according to EN 1057, quality assured
- Made of pure copper Cu-DHP
- With quality mark and DVGW certification: DV-7204AU2106 (6 to 159 mm outside diameter)
- Universal use in a range of finely differentiated dimensions
- Optimum availability and compatibility with a wide range of fittings
- Maximum operating temperature at 10 bar operating pressure: 250 °C (applies to dimensions up to DN 150)
- Fire resistance: EN 13501-1 – A1 (nonflammable)
- Dimensions according to DVGW GW 392 (6 to 159 mm) with closed tube ends
- For optimal drinking water hygiene
*Mass balance approach, based on ISO 14021, verified by TÜV SÜD.
Reliable for all areas of home installation
For many years, installers have been relying on SANCO branded copper tubes. The tubes are very reliable, suitable for all areas of domestic installation and have more than proven their worth in practice. Whether drinking water supply (hot and cold), heating systems, oil, gas and liquid gas supplies as well as thermal solar systems: Wieland SANCO tubes are always the right choice and, of course, covered by the relevant regulations.
Technical features
- Patented manufacturing process: SANCO tubes are significantly better than required by standards and regulations.
- Design according to EN 1057, quality assured
- Made of pure copper Cu-DHP
- With quality mark and DVGW certification:
DV-7204AU2106 (12 to 159 mm outside diameter). - Universal use in a range of finely differentiated dimensions
- Optimum availability and compatibility with a wide range of fittings
- Maximum operating temperature: 250 °C
- Fire resistance: EN 13501-1-A1 (non-flammable)
- Dimensions according to DVGW GW 392 (12 to 159 mm) with closed tube ends
- For optimal drinking water hygiene
- Wide range of certifications available, such as Kitemark, Afnor, KIWA, DVGW and many others
Fields of application
- Domestic hot and cold water supply
- Heating systems
- Gas and oil services for heating and cooking
- Solar systems
- Rainwater
- Industrial compressed air
- Sprinkler and Fire-fighting-systems
- Further applications in consultation with our technical advisory service
WICU
WICU tubes a have a mill-applied protective coating. They are therefore suitable for concealed installation under plaster or in environments with an aggressive atmosphere, and for installation outdoors, either above or below ground.
Technical features
- Design according to EN 1057, quality assured
- Made of pure copper Cu-DHP
- With quality mark and DVGW certification:
- DV-7204AU2106 (12 to 42 mm outside diameter).
- Protective coating conforms to EN 13349 and DIN 30672-1 class B
- Reduction of condensation
- Fire resistance: EN 13501-1-E
- Color of coating: light gray
- Temperature range up to 100 °C
Fields of application
- Domestic hot and cold water supply
- Heating systems
- Gas and oil services for heating and cooking
- Rainwater
- Industrial compressed air
- Further applications in consultation with our technical advisory service
WICU Flex
WICU Flex is a plumbing tube with a flexible coating for rapid installation. The coating consists of closed-cell PE foam covered by a structured protective film. WICU Flex is supplied in coils for rapid connection to manifolds etc. and for underfloor installations.
Technical properties
- Design according to EN 1057, quality assured
- Made of pure copper Cu-DHP
- With quality mark and DVGW certification:
DV-7204AU2106 (12 to 22 mm outside diameter) - CFC/FKW-free polyethylene foam (PE) with a
- PE structural foil
- Sound insulation: DIN 4109 - A1
- Thermal conductivity of the insulation layer according to DIN 52613:
= 0.040 W/mK at 40 °C - Fire resistance: N 13401-1-E
- Color of coating: white
- Temperature application range: up to 100 °C
Fields of application
- Connecting tubes
- Domestic hot and cold water supply
- Central heating systems
cuprotherm CTX
cuprotherm CTX tubes are copper tubes with a firmly adhering coating. Due to their structure, they are very easy to process and are characterized by a flexibility so far unknown for metal tubes. CTX tubes are a technically high-quality and at the same time economically interesing solution: They offer an attractive price per meter for copper tubes at stable conditions, and are therefore also convincing in terms of reliability in planning.
Technical features
- Flexible copper tube made of pure copper Cu-DHP
- Temper: soft R220 according to EN 1057 with firmly adhering coating made of PE-RT
- Fire behavior EN 13501-1, class E
- Color of the coating: white, similar to RAL 9010 (pure white)
- Temperature application range: up to 100 °C
Fields of application
- Heating
- Cooling
- Radiator connection
- Rainwater harvesting systems
- Ground collectors (water/glycol)
- Concrete core activation
cuprotherm.plus
cuprotherm is Europe's most frequently installed copper underfloor heating system, and for good reason. The outstandingly long service life of cuprotherm copper tubes will make you forget about surface heating for decades after it has been installed. Due to the highest thermal donductivity in technical materials, efficient use for this application is also good for the wallet in the long run.
The orange coating provides mechanical and chemical protection from the outside and allows the cuprotherm tube to expand unhindered in length when the temperature changes.
Technical properties
- Design according to EN 1057
- Fire resistance: EN 13501-1-E
- Building material class: DIN 4102 - A1
- With quality mark
- Diffusion rate: 0.00 mg/m²*d after 50 years
Fields of application
- Surface heating and cooling
- Wall heating
- Industrial surfaceheating
- Sports floor heating
cuprotherm.blank
cuprotherm is Europe's most frequently installed copper underfloor heating system, and that for good reasons. The oustandingly long service life of cuprotherm copper tubes will make you forget about surface heating for decades after it has been installed. Due to the highest thermal conductivity in technical materials, efficient use for this application is also good for the wallet in the long run.
The bare copper tube also withstands high temperatures and is therefore the first choice in applications with mastic asphalt.
Technical properties
- Design according to EN 1057
- Fire resistance: EN 13501-1-A1 (non-flammable)
- With quality mark
- Diffusion rate: 0.00 mg/m²*d after 50 years
Fields of application
- Underfloor heating with mastic asphalt screed
- Wall heating with clay plaster
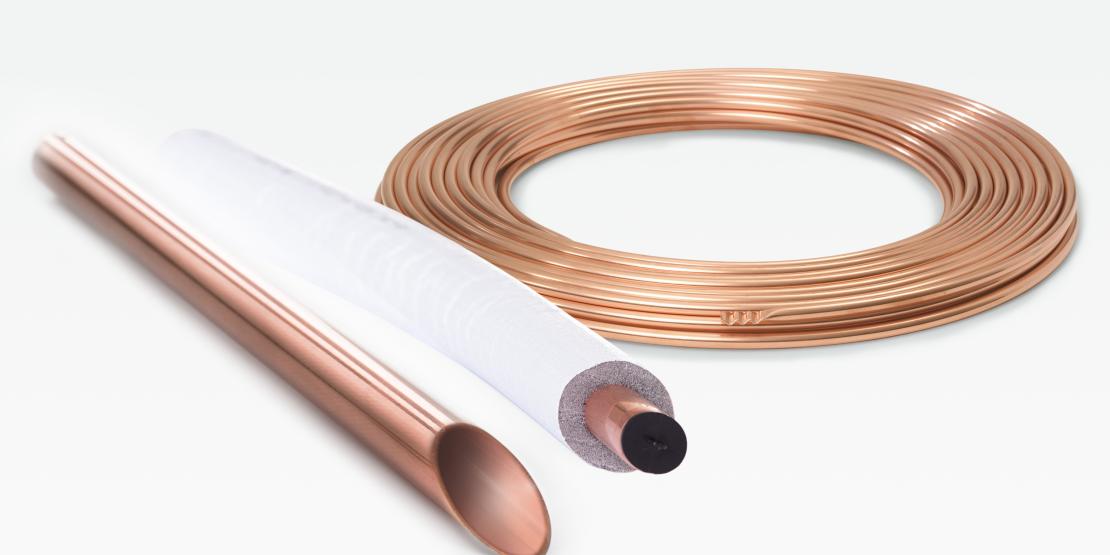
Materials
K65 - Sustainable and efficient
two keywords that have had a decisive impact on our time and have gained in relevance in recent years, especially in refrigeration. Increased environmental awareness in society and industry has therefore led to a kind of renaissance of natural refrigerants, especially CO2. Wieland supports this turnaround with a tube system that meets the high requirements of CO2 as a refrigerant.
Wieland K65 tubes have been designed for CO2 applications in the commercial field, especially that of supermarket refrigeration systems. Wieland K65 alloy provides the mechanical strength high enough to withstand the high operating pressures of CO2. At the same time, K65 tubes have outstanding processing properties, similar to those of standard copper (Cu-DHP/C12200).
Wieland K65 tubes are offered from stock in two pressure ranges, 80 bar and 120 bar, and in dimensions ranging from 3/8” up to 2-1/8”.
All Wieland K65 tubes are available in the soft condition (R300/O61) to ensure excellent bending / flaring and collaring properties.
Other dimensions and delivery forms such as level wound coils are offered for industrial processing, in particular manufacturing of CO2 heat exchangers (evaporator/gas cooler).
More K65 products in other categories
Your benefits
- Cost reduction through weight reduction
- Proven processing technology: brazing instead of welding!
- Economical and safe installation of regrigeration systems with up to 120 bar operation pressure
- Excellent heat transfer
- Design according to EN 14276
Typical applications
- Pipelines for refrigeration systems, in particular for CO2 refrigerant, with an operation pressure of up to 120 bar
Technical properties
- Material: K65
- Operation pressure: 80 bar and 120 bar
- Condition: soft R300/O61
- Delivery form: straight lengths of 5 m
- Available dimensions: 9,52 - 53,97 mm (3/8" - 2-1/8")
- Tube ends: closed
- Usual standards: EN 14276 / EN 12735-1
Further information
cuprofrio.plus
Wieland branded copper tubes cuprofrio and cuprofrio.plus have a high level of internal cleanliness due to the individually closed tube ends and are suitable for refrigerants according to EN 12735-1.
cuprofrio tubes can be easily processed on site and conform to high quality standards with their extremely clean and dry inner surface. Close tube ends ensure the required quality even during storage and transportation.
learn more
cuprofrio.plus
cuprofrio.plus-tubes are insulated on the outside, which prevents nearly all water condensation on the outer surface of the tube.
Your benefits
- clean and dry inside surface
- standard dimensions available from stock
- good processing, easy joining, very easy to unwind and bend
- resistant, colour-fast insulation ensures consistent material properties in all weather conditions
- prevention of condensation water through insulating layer
- supplier traceability through signature
- compliance with Pressure Equipment Directive 97/23/EC
Fields of application
cuprofrio is suitable for technical gases and liquids, for example in
- chillers
- air-conditioning and refrigeration units
- heat exchangers
cuprofrio – refrigeration
Wieland branded copper tubes cuprofrio and cuprofrio.plus have a high level of internal cleanliness due to the individually closed tube ends and are suitable for refrigerants according to EN 12735-1.
cuprofrio tubes can be easily processed on site and conform to high quality standards with their extremely clean and dry inner surface. Close tube ends ensure the required quality even during storage and transportation.
learn more
Your benefits
- clean and dry inside surface
- closed tube ends in order to maintain cleanliness
- supplier traceability through signature
- standard dimensions available from stock
- good processing, easy joining, very easy to unwind and bend
- tube quality according to EN 12735-1
- compliance with Pressure Equipment Directive 2014/68/EU
Fields of application
cuprofrio is suitable for technical gases and liquids, for example in
- chillers
- air-conditioning and refrigeration units
- heat exchangers
Forms of delivery
- Coils (pancakes)
- Straight lengths of 5 m
cupromed – medical gas supply
The seamless drawn cupromed copper tube is used for refrigeration/air conditioning as well as for medical gas supply units according to EN ISO 7396-1. cupromed tubes in straight lengths meet the requirements according to EN 13348 and those according to EN 12735-1.
Your benefits
- clean and dry inside surface
- closed tubes ends keep the surface clean
- supplier traceability through signature
- standard dimensions available from stock
- good processing, easy joining, very easy to unwind and bend
- standard tube quality according to EN 12735-1
- compliance with Pressure Equipment Directive 2014/68/EU
- Requirements according to the PED/Pressure Equipment Directive 2014/68/EU
Fields of applications
cupromed is suitable for the transportation of technical gases and liquids as well as medical gas and vacuum in
- medical gas supply units
- refrigeration and air conditioning units
cuprogeo – geothermal energy
The seamless drawn cuprogeo tube is used for geothermal energy production. cuprogeo is designed for the use of refrigerants and gases for direct evaporation in heat pumps. The advantage of this application is that high performance can be achieved with suitable heat pumps.
Your benefits
- clean and dry inner surface
- supplier traceability through signature
- tube protected by an outside surface coating
- standard tube quality according to EN 12735-1
- requirements comply with the Pressure Equipment Directive 2014/68/EU
Fields of application
- geothermal energy
- refrigeration equipment and heat exchangers
- geothermal heat pumps with direct evaporation
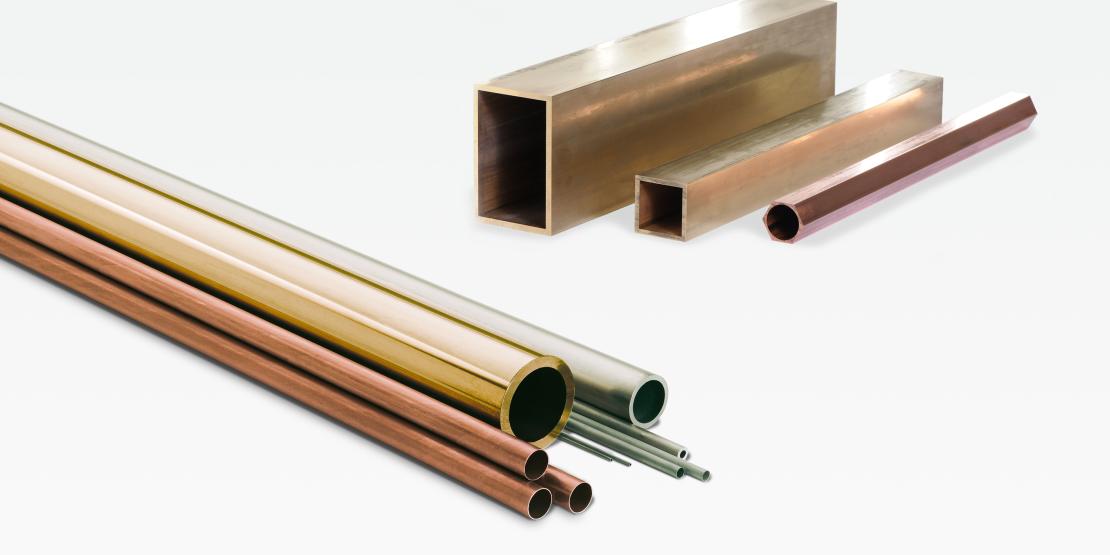
From the broad spectrum of our alloy portfolio, we manufacture tubes to customer specifications and the highest quality standards in accordance with individual requirements for a wide range of applications.
We manufacture alloy tubes in straight lengths for you. We can supply almost any dimension in a wide range of alloys, from 3 mm outside diameter to large-diameter tubes with an outside diameter of approx. 320 mm. All tubes are drawn seamless, high precision and constant properties are a matter of course.
We would be pleased to work out the optimum solution for your application together with you.
You do not need a round tube but a profile tube? - Please contact us! With our interdisciplinary team of experts we will find a solution.
Materials
What is a profile tube?
Profile tubes are manufactured from round pressed or also drawn tubes. Depending on the requirements, the final shape is produced by cold forming in various processing steps.
produced. This makes sectional tubes a sensible, cost-effective addition to conventional
extruded profiles.
Complex geometries, thin walls, high precision.
Areas of application
Wieland sectional tubes made of copper materials are mainly used in industries that place special demands on the material and have to ensure high reliability of the end product
reliability of the end product: These include electronics and electrical engineering, the sanitary industry or architecture.
Other possible applications for our profile tubes are in model making, medical technology, automotive engineering and the manufacture of writing instruments or musical instruments. In particular
For foundry applications, Wieland also manufactures large, square or round profile tubes for ingot molds.
Dimensions
Production is carried out according to your drawing.
Profile tubes can be manufactured from round tubes with a diameter of 5 mm up to a diameter of 230 mm. Depending on the alloy or diameter, the wall thickness may be
can be selected between 0.1 mm and 15 mm. The inner cross-section must be at least 5 mm2 and the smallest diameter of the circumscribed circle at least
5 mm. The ratio of the largest circumscribing circle to the smallest wall thickness must not exceed 125:1. We supply profiled tubes up to 10 m long, in exceptional cases up to
in exceptional cases up to 18 m.
Materials
Starting materials for sectional tubes are primarily copper materials or lead-free brasses. Depending on the application, other material groups may also be used:
- leaded machining brasses
- special alloys
- tin bronzes
- New silver
The good cold formability of the material extends the design possibilities for the
in the design of the sectional tubes.
Depending on the application and the resulting requirements on the material
on the material, the profiles can be designed in different strength states
from soft to hard;
We will be pleased to advise you on our alloys and dimensions
We manufacture seamless tubes with outer diameters up to 320 mm. They are suitable for electrical engineering and telecommunications, heat transfer and apparatus engineering.
Low-alloy copper materials with higher strength serve as brake line tubes in motor vehicles.
We have specialties such as dezincification-resistant materials in our range, and alloys with high wear resistance, as used in crude oil production.
Handrails, shower bars, towel rails, handgrip elements, water inlets and outlets, drains, decorative claddings: For these and many other products, the metal
The metal goods industry uses tubes made of copper alloys for these and many other products.
Safely protected !
The packaging
By choosing the right packaging, your individual needs for transport, storage and processing can be taken into account.
Thus, the excellent product quality is preserved and a comfortable processing is made possible.
Based on our experience, we offer you proven packaging materials - we are also happy to find an individual solution.
Each package is labeled on the front side to ensure clear identification and traceability.
Sustainable by conviction:
Wieland uses reusable packaging for the most part to protect the environment.
This also benefits you - you save disposal costs.
Typical packaging forms for tubes and profile tubes in straight lengths
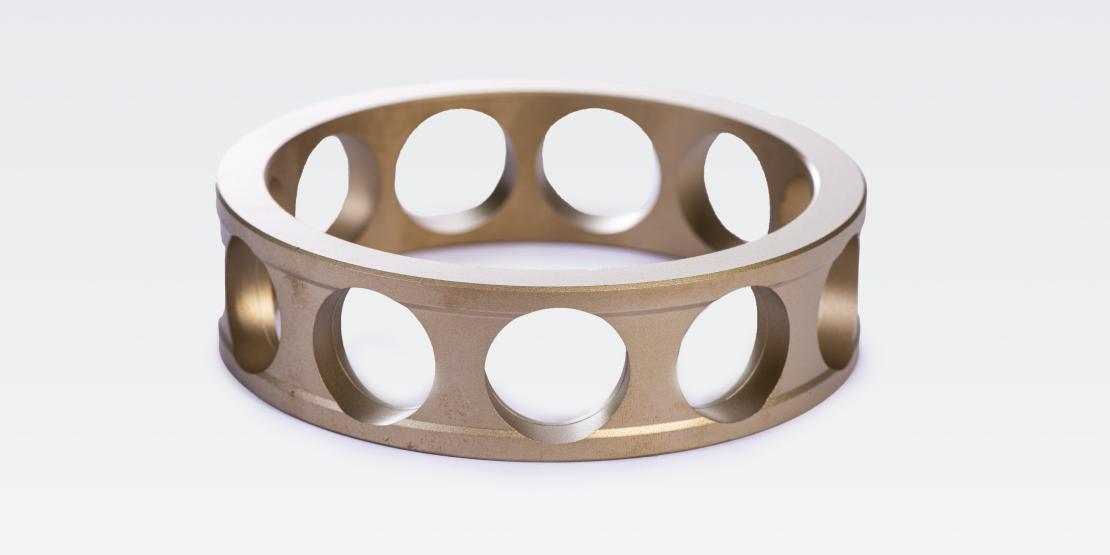
Our ball bearings are available as
- Deep groove ball bearings
- Angular contact ball bearings
- Thrust ball bearings
- Angular contact thrust ball bearings
- Four point contact ball bearing
Description | Rm N/mm2 | HB2,5/62,5 | |
Brass | Z49 – CuZn40Pb2 | ≥380 | 80-120 |
Brass | S38 – CuZn40Al1Pb | ≥415 | 95-133 |
Brass | Z51 – CuZn39Pb1Al | ≥390 | 90-120 |
Brass (lead-free) | SC6 – leadfree | ≥500 | ≥105 |
Aluminiumbronze wrought (lead-free) | U39 – CuAl10Ni5Fe4 | ≥650 | - |
Aluminiumbronze casted (lead-free) | U44 – CuAl10Fe5Ni5-GZ | ≥650 | ≥150 |
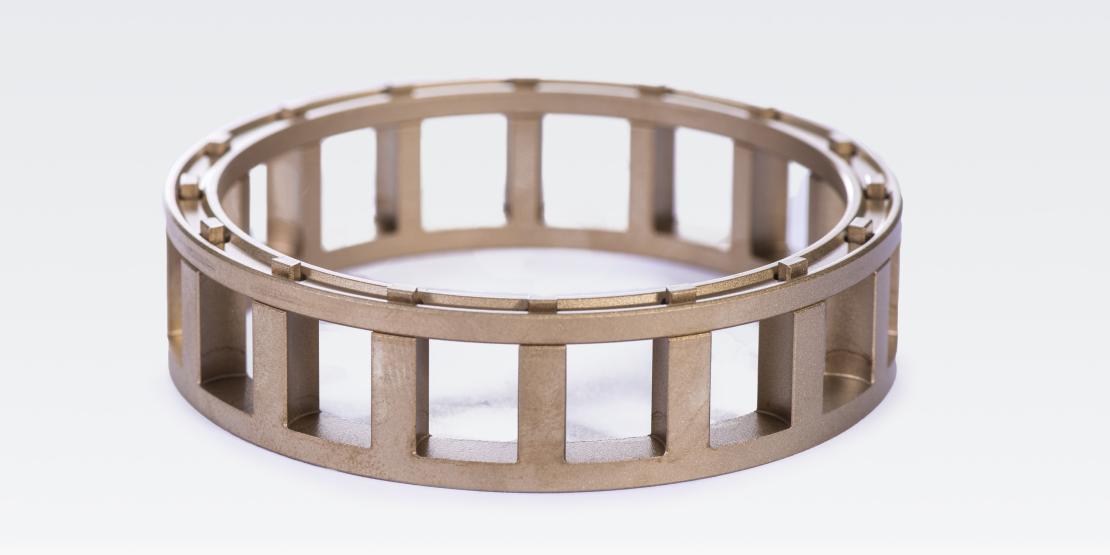
Our roller bearings are available as
- Cylindrical roller bearings
- Needle roller bearings
- Tapered roller bearings
- Spherical roller bearings
- Thrust bearings (cylindrical-, needle-, tapered-, or spherical roller)
Description | Rm N/mm2 | HB2,5/62,5 | |
Brass | Z49 – CuZn40Pb2 | ≥380 | 80-120 |
Brass | S38 – CuZn40Al1Pb | ≥415 | 95-133 |
Brass | Z51 – CuZn39Pb1Al | ≥390 | 90-120 |
Brass (lead-free) | SC6 – leadfree | ≥500 | ≥105 |
Aluminiumbronze wrought (lead-free) | U39 – CuAl10Ni5Fe4 | ≥650 | - |
Aluminiumbronze casted (lead-free) | U44 – CuAl10Fe5Ni5-GZ | ≥650 | ≥150 |
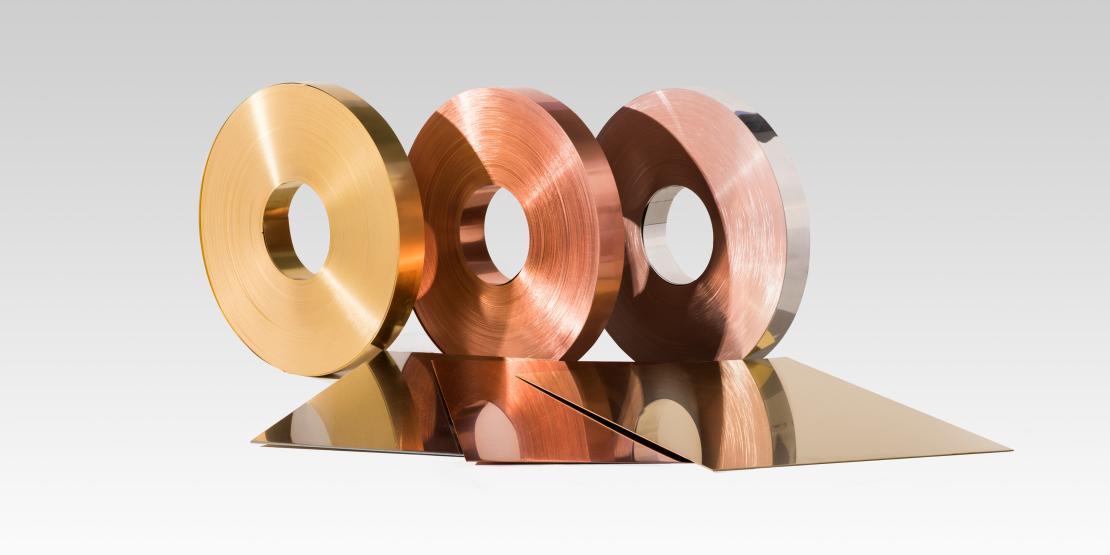
The surface quality depends greatly on the roughness. We offer the following roughnesses as standard:
Maximum value Special tolerance (µm) | Maximum value Special tolerance I (µm) | Maximum value Special tolerance II (µm) | ||||
Thickness (mm) | Ra | Rmax | Ra | Rmax | Ra | Rmax |
0.1 - 0.4 | 0.25 | 2 | 0.18 | 1.4 | 0.13 | 1 |
0.4 - 1.0 | 0.25 | 2 | 0.2 | 1.6 | 0.18 | 1.4 |
1.0 - 1.5 | 0.5 | 2 | - | - | 0.2 | 1.6 |
1,5 - 3,0 | 0,3 | 3 | * | * | * | * |
Modification possible due to alloy or thickness
If you wish the end products to fulfil high visual requirements, we can offer you a range of special qualities to choose from:
- for mirror finishing
- for electrolytic polishing
- for etching
- bright rolled
- mirror finish rolled
- free of flow lines
These special products set certain restrictions on the range of geometries. Our experts will be pleased to advise you on the surface qualities best fulfilling your requirements.
In electrical and electronic applications, contact resistance plays a crucial role. The formation of oxide layers can compromise this severely and may cause contact failure. As a rule, therefore, at least the contact zones are coated. The most common coatings are of tin or tin alloys. Our products are treated on ultra modern hot dip tinning plant. A range of tin plated variants are possible, depending on the customer’s requirements.
We can also offer strips with full or selective silver or nickel plating. These strips you can purchase directly from us as a single source. They are finished at external partner companies.
Sheets and strips may be provided with a protective film of PE that protects the surfaces against mechanical damage during downstream machining processes. The film is attached with an acrylic adhesive and can be drawn off after processing.
Sizes of strip with a protective coating | ||
Thickness (mm) | Width (mm) | Coating |
0,3 - 2,0 | 30 - 700 | single- or double-sided |
Sizes of sheet with protective coating | |||
Thickness (mm) | Width (mm) | Length (mm) | Coating |
0,3 - 1,0 | 500 - 800 | 500 - 3.000 | single- or double-sided |
1,0 - 10,0 | 500 - 1.250 | 500 - 4.000 | single- or double-sided |
Sizes of strip cut to length with protective coating | |||
Thickness (mm) | Width (mm) | Length (mm) | Coating |
0,3 - 1,0 | 150 - 500 | 700 - 2.500 | single-sided |
1,0 - 10,0 | 20 - 500 | 200 - 4.000 | single-sided |
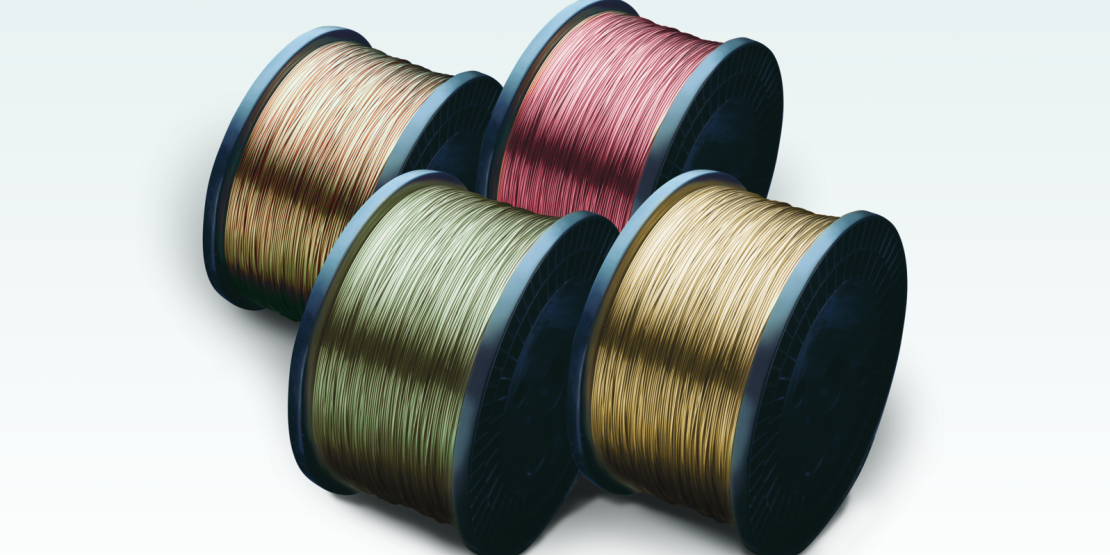
Materials
Wieland | EN Designation | EN No. | ASTM UNS-No. |
---|---|---|---|
K10 | Cu-OFE | CW009A | - |
K12 | Cu-HCP | CW021A | C10300 |
K18/K32 | Cu-ETP | CW004A | C11000 |
K30 | Cu-OF | CW008A | C10200 |
Wieland | EN Designation | EN No. | ASTM UNS-No. |
---|---|---|---|
K41 | CuNi1Pb1P* | - | C19150 / C19160 |
K65 | CuFe2P | CW107C | C19400 |
K81 | CuSn0,15 | CW117C | C14415 |
KC1 | CuPb1P | CW113C | C18700 |
eco KS2® | CuSP | CW114C | C14700 |
Wieland | EN Designation | EN No. | ASTM UNS-No. | JIS-No. |
---|---|---|---|---|
Z11 | CuZn35Pb1 | CW600N | C34000 | |
Z12 | CuZn35Pb2 | CW601N | C34200 / C34500 | |
Z21 | CuZn38Pb2 | CW608N | C3713 | |
Z23 | CuZn36Pb3 | CW603N | C36000 | |
Z29 | CuZn39Pb2 | CW612N | C37700 | |
Z31/Z41/Z48 | CuZn40Pb2 | CW617N | C38000 | |
Z32/Z33 | CuZn39Pb3 | CW614N | C38500 | |
Z40 | CuZn43Pb2Al | CW624N | - | |
Z45/Z46 | CuZn36Pb2As | CW602N | C35330 |
Wieland | EN Designation | EN No. | ASTM UNS-No. | JIS-No. |
---|---|---|---|---|
M10 | CuZn10 | CW501L | C22000 | C2200 |
M15/M16/M17 | CuZn15 | CW502L | C23000 | |
M20 | CuZn20 | CW503L | C24000 | C2400 |
M36 | CuZn36 | CW507L | C26800 / C27000 | C2700 |
M37/M38 | CuZn37 | CW508L | C27200 | C2720 |
eco M41® | CuZn38As | CW511L | C27453 | |
eco M57® | CuZn42 | CW510L | - | |
eco M58® | CuZn42 | CW510L | - |
Wieland | EN Designation | EN No. | ASTM UNS-No. |
---|---|---|---|
S40 | CuZn37Mn3Al2PbSi | CW713R | C67420 |
eco S34® | CuZn34Mn2SiAlNi* | - | C67340 |
eco SW1® | CuZn21Si3P | CW724R | C69300 |
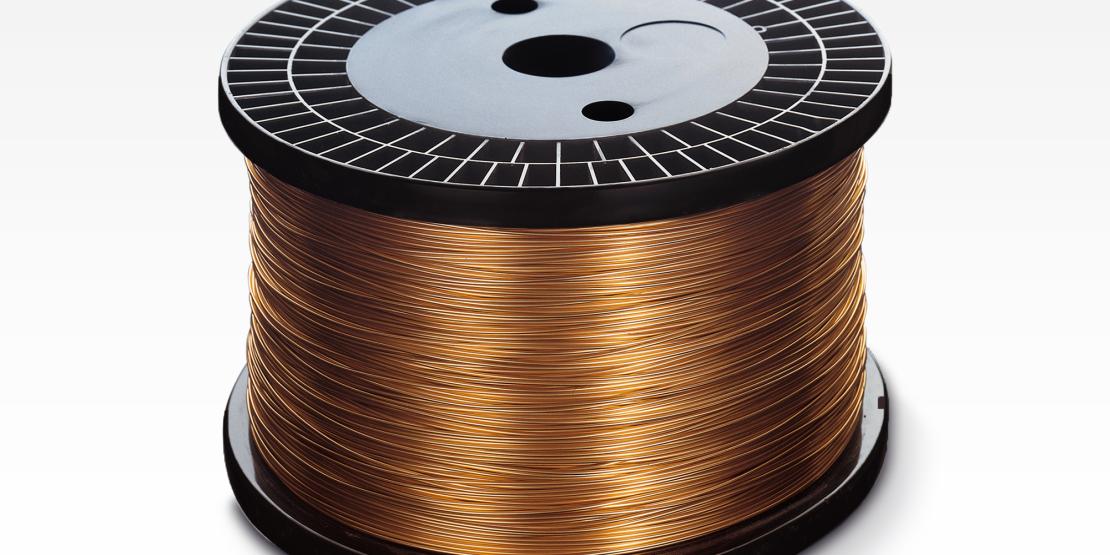
Electrical and electronic applications often require materials that combine good electrical and mechanical properties. The wide range of Wieland alloys provides the optimal material for each and every application.
Learn more about
WITRONIC
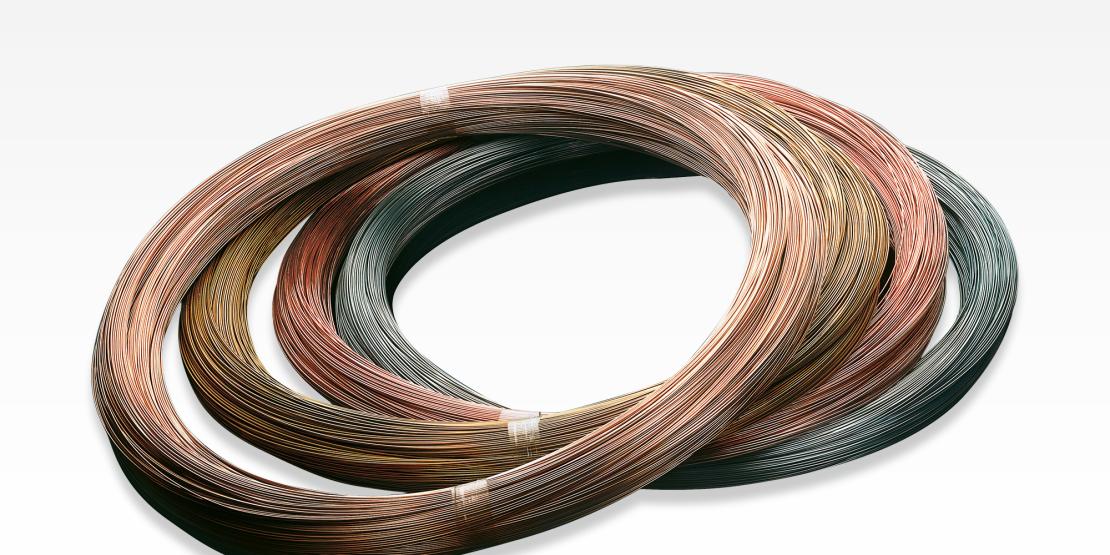
The Wieland WICONNEC brand offers a range of copper materials in the form of bars and wires that are ideal for machined sockets and pins for plug connectors. This material portfolio also offers low cost brass materials in addition to specially developed copper alloys for complex applications.
Learn more about
WICONNEC
Resources
Information material and important documents for download
279.29 KiB
177.27 KiB
286.93 KiB
230.23 KiB
Production of copper alloys and copper semi-finished products
1.59 MiB
Production of copper alloys and copper semi-finished products
1.59 MiB
71.24 KiB
289 KiB
Wieland Gruppe
2.31 MiB
Wieland Group
2.3 MiB
Wieland-Werke AG
185.21 KiB
Wieland Group
66.62 KiB
Wieland Group
141.72 KiB
Coppper and Copper Alloy tubes
191.77 KiB
532.06 KiB
577.3 KiB
518.06 KiB
620.17 KiB
511.01 KiB
571.51 KiB
578.18 KiB
550.88 KiB
584.6 KiB
634.97 KiB
601.19 KiB
583.04 KiB
291.99 KiB
153.84 KiB
167.59 KiB
Wieland Group
251.64 KiB
Wieland Group
254.7 KiB
Wieland-Werke AG, Ulm
139.87 KiB
Wieland-Werke AG, Ulm
40.17 KiB
Wieland-Werke AG, Ulm
48.04 KiB
Wieland-Werke AG, Ulm
134.94 KiB
Wieland Group
419.13 KiB
Wieland Group
421.38 KiB
Wieland Group
421.02 KiB
Thermal Solutions
3.49 MiB
Thermal Solutions I Enhanced Heat Transfer with Carbon Steel Tubes in Buffer Tanks
156.48 KiB
Thermal Solutions
157.26 KiB
Thermal Soltutions I For absolutely reliable media separation with best thermal contact
3 MiB
Thermal Solutions I Enhanced boiling tube for the hydrocarbon industry
201.1 KiB
Thermal Solutions
3.12 MiB
Thermal Solutions
3.34 MiB
Thermal Solutions
938.1 KiB
Thermal Solutions
349.02 KiB
Thermal Solutions
3.51 MiB
Thermal Solutions I Trufin & TurboChil
545.95 KiB
Thermal Solutions I Trufin & TurboChil
347.62 KiB
Thermal Solutions I Trufin & TurboChil
476.57 KiB
Thermal Solutions I Trufin & TurboChil
329.92 KiB
Thermal Solutions I Genau so, wie es für Sie am besten passt
372.53 KiB
Thermal Solutions I sicher. effizient. ökologisch
310.51 KiB
Thermal Solutions I For more efficiency
1.48 MiB
Thermal Solutions I safe. efficient. ecological.
310.67 KiB
Thermal Solutions I Optimized solutions that best suit your needs
369.57 KiB
Thermal Solutions I For Greater Effiency
3.56 MiB
635.67 KiB
639.09 KiB
Extruded Products, Thermal Solutions, RD&I
638.84 KiB
634.19 KiB
Extruded Products, Thermal Solutions, RD&I
1.89 MiB
Extruded Products, Thermal Solutions, RD&I
1.89 MiB
Rolled Products
1.94 MiB
Rolled Products
1.93 MiB
Rolled Products
736.64 KiB
262.26 KiB
261.51 KiB
247.99 KiB
Wieland Group
1.24 MiB
Wieland Group
1.23 MiB
Wieland Group
997.69 KiB
Wieland Group
989.36 KiB
Wieland-Werke AG
1.07 MiB
Wieland-Werke AG
1.07 MiB
865.57 KiB
943.51 KiB
425.27 KiB
Wieland K75, die hochleitfähige Hochleistungs-Kupferlegierung
999.32 KiB
Wieland K75 high-conductivity high-performance copper alloys
1.01 MiB
Wieland K58 for miniaturized connector springs
1.39 MiB
1.07 MiB
Wieland-Werke AG
1.07 MiB
1.07 MiB
1.07 MiB
1.07 MiB
1.07 MiB
Wieland K58 for miniaturized connector springs
1.41 MiB
Rolled Products
3.78 MiB
Wieland-Werke AG
3.05 MiB
3.05 MiB
3.05 MiB
3.05 MiB
Rolled Products
3.77 MiB
3.05 MiB
3.05 MiB
3.05 MiB
1.99 MiB
3.05 MiB
WICONNEC
2.93 MiB
Wieland-Werke AG
59.81 KiB
Wieland-Werke AG
53.88 KiB
WICONNEC
2.89 MiB
The Game Changer
241.18 KiB
WITRONIC
5.1 MiB
WITRONIC
5.1 MiB
W5000
937.31 KiB
W5006
607.09 KiB
W5000
936.09 KiB
W5006
604.01 KiB
Wieland-Werke AG, Ulm: Copper and copper alloy tubes
128.49 KiB
148.81 KiB
377.2 KiB
197.79 KiB
127.97 KiB
346.98 KiB
Wieland-Werke AG
344.49 KiB
Wieland-Werke AG, Ulm: Aluminium Alloy Plates, Sections, Bars, Castings & Forgings
329.83 KiB
Wieland-Werke AG, Ulm: Copper Alloy Tubes
330.07 KiB
Wieland L96, die grüne Alternative zu Kupferlegierungen mit Beryllium
627.09 KiB
Wieland L96, the green alternative to beryllium coppers
215.25 KiB
199.75 KiB
201 KiB
1.08 MiB
1.08 MiB
712.05 KiB
704.12 KiB
Wieland K55 R800 hochfester Zustand in großen Banddicken
769.8 KiB
B16 SUPRALLOY® feinkörnige Bronze jetzt verfügbar in für Einpress-Verbinder üblichen Dicken
627.91 KiB
Copper alloys for drinking water applications
6.57 MiB
Copper alloys for drinking water applications
6.57 MiB
B16 SUPRALLOY® fine grain bronze strip now available in press-fit-thickness
217.64 KiB
1.79 MiB
Rolled Products
1.83 MiB
Rolled Products
1.83 MiB
1.79 MiB
Lagerfähigkeit, Lötbarkeit und Anlaufbeständigkeit
6.19 MiB
Wieland K55 R800 high-strength temper in high strip thickness
149.38 KiB
Visual appearance and solderability
643.73 KiB
Visual appearance and solderability
6.19 MiB
703.16 KiB
282.08 KiB
Wieland K75 high-conductivity high-performance copper alloys
549.05 KiB
Wieland K58 high-strength copper alloys serves miniaturized connector springs
806.95 KiB
Production of copper alloys and copper semi-finished products
359.99 KiB
Hot dip tinned copper and copper alloy strip
701.17 KiB
B16 SUPRALLOY® fine grain bronze strip now available in press-fit-thickness
486.74 KiB
Wieland L96, the green alternative to beryllium coppers
425.19 KiB
Wieland K55 R800 high-strength temper in high strip thickness
343.81 KiB
Copper alloy sheets and plates
589.92 KiB
Strip for connectors
850.06 KiB
Production of copper alloys and copper semi-finished products
359.99 KiB
For presentation to the export control authorities of the Federal Republic of Germany
170.68 KiB
Wieland Gruppe
845.65 KiB
Wieland Group
14.03 MiB
13.96 MiB
308.12 KiB
285.34 KiB
283.2 KiB
Wieland Group
317.52 KiB
Wieland-Werke AG, Ulm: Production of copper alloys and copper semi-finished products
1.59 MiB
Rolled Products
8.35 MiB
Wieland-Werke AG, Ulm: Production of copper alloys and copper semi-finished products
1.59 MiB
Rolled Products
7.9 MiB
Wieland Asia
371.11 KiB
Wieland-Werke AG, Voehringen
1.53 MiB
257.4 KiB
230.57 KiB
Wieland Groupe
422.58 KiB
Wieland Group
5.2 MiB
Wieland Group
5.22 MiB
Portugal 2020 Project Discription
224.12 KiB
Lead-free brass strip, sheets and plates for a sustainable future
969.98 KiB
Lead-free brass strip, sheets and plates for a sustainable future
939.49 KiB
1.13 MiB
Thermal Solutions I Condenser and Evaporator with optimum counter-flow layout
702.57 KiB
1.31 MiB
Wieland Group
1.31 MiB
Thermal Solutions I Condenser and Evaporator with optimum counter-flow layout
706.45 KiB
Thermal Solutions I High finned tubes for signifcantly enlarged outside surface
1.03 MiB
Thermal Solutions I High finned tubes for signifcantly enlarged outside surface
1.59 MiB
Extruded Products
6.64 MiB
Thermal Solutions I Medium-high finned tubes for compact coiled and bent heat exchangers
570.89 KiB
Extruded Products
6.64 MiB
Thermal Solutions I
1.33 MiB
Wieland Group
3.88 MiB
Wieland Group
3.87 MiB
2.79 MiB
367.74 KiB
186.54 KiB
1.44 MiB
1.45 MiB
971.59 KiB
1.89 MiB
1.89 MiB
1.05 MiB
1.58 MiB
1.06 MiB
1.58 MiB
3.17 MiB
15.51 MiB
3.11 MiB
666.39 KiB
667.52 KiB
90.77 KiB
93.67 KiB
4.82 MiB
901.38 KiB
1.1 MiB
1.49 MiB
1.99 MiB
1.02 MiB
946.76 KiB
2.34 MiB
4.86 MiB
13.53 MiB
13.63 MiB
ecoline_Die-bleifreien-Legierungen
5.36 MiB
ecoline_The-lead-free-alloys
5.34 MiB
1.62 MiB
1.62 MiB
Wieland Group
1.57 MiB
Wieland Group
1.57 MiB
Wieland Group
824.17 KiB
3.85 MiB
Stock Program Vöhringen
1.91 MiB
Lagerprogramm Vöhringen
1.91 MiB
Rolled Products
2.13 MiB
Rolled Products
2.13 MiB
Wieland-Werke AG
Graf-Arco-Straße 36
89079 Ulm
Germany
Executive Board:
Dr. Erwin Mayr, CEO
Gregor Tschernjavski, CFO
Chairman of the Supervisory Board:
Fritz-Jürgen Heckmann
Headquarters: Ulm
Court of registration: Ulm, HRB 1256
VAT identification number: DE811147730
Career
Start your career at Wieland-Werke AG
Unleash potential.

Already know your search term? Then go ahead and use our full text search. You will get a list of all relevant results.